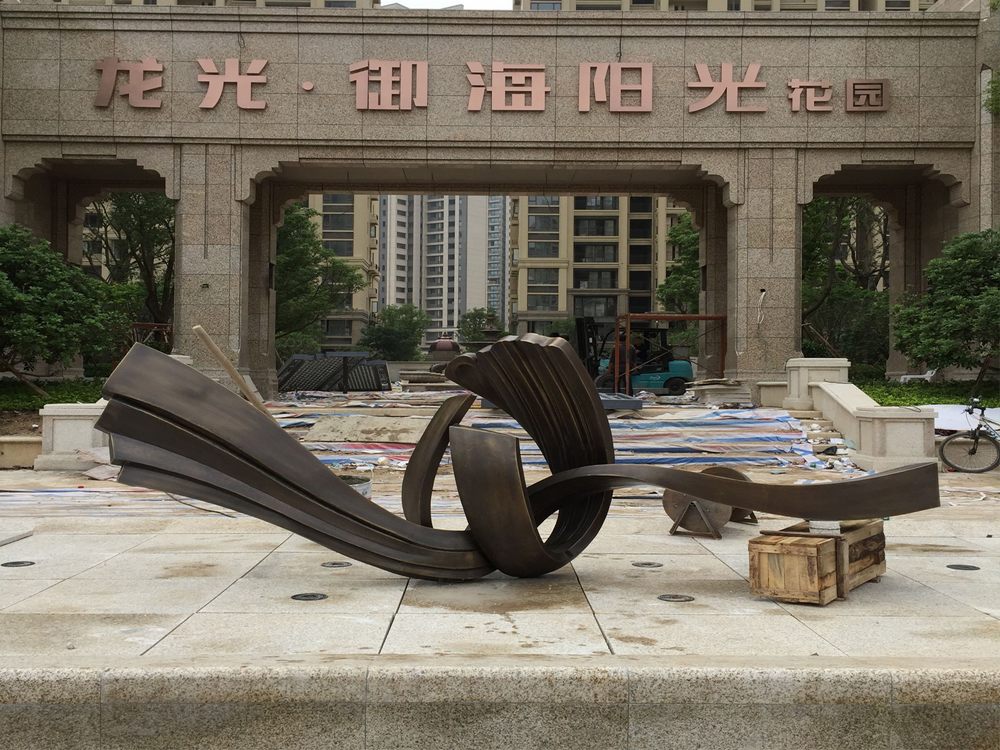
Bronze annealing, a critical heat treatment process, has evolved significantly over time. Traditional methods relied on slow, manual heating in charcoal or wood-fired furnaces, requiring skilled artisans to monitor temperature visually. These processes often took hours or even days, with inconsistent results due to uneven heat distribution.
Contemporary annealing, by contrast, utilizes electric or gas-fired kilns with precise digital temperature controls, reducing processing time to minutes or hours. Modern techniques also incorporate protective atmospheres to prevent oxidation, a common issue in traditional methods. Advanced technologies like induction heating allow for targeted annealing of specific sections, impossible with older approaches.
Energy efficiency marks another key difference. Traditional annealing wasted significant heat, while modern systems recycle thermal energy. Additionally, contemporary methods enable repeatable, standardized results crucial for industrial applications, whereas traditional annealing often produced unique variations.
Despite these advancements, some artisans still prefer traditional methods for certain artistic bronze works, valuing the subtle imperfections they introduce. Understanding these differences helps craftsmen and manufacturers choose the most suitable approach for their specific bronze applications.