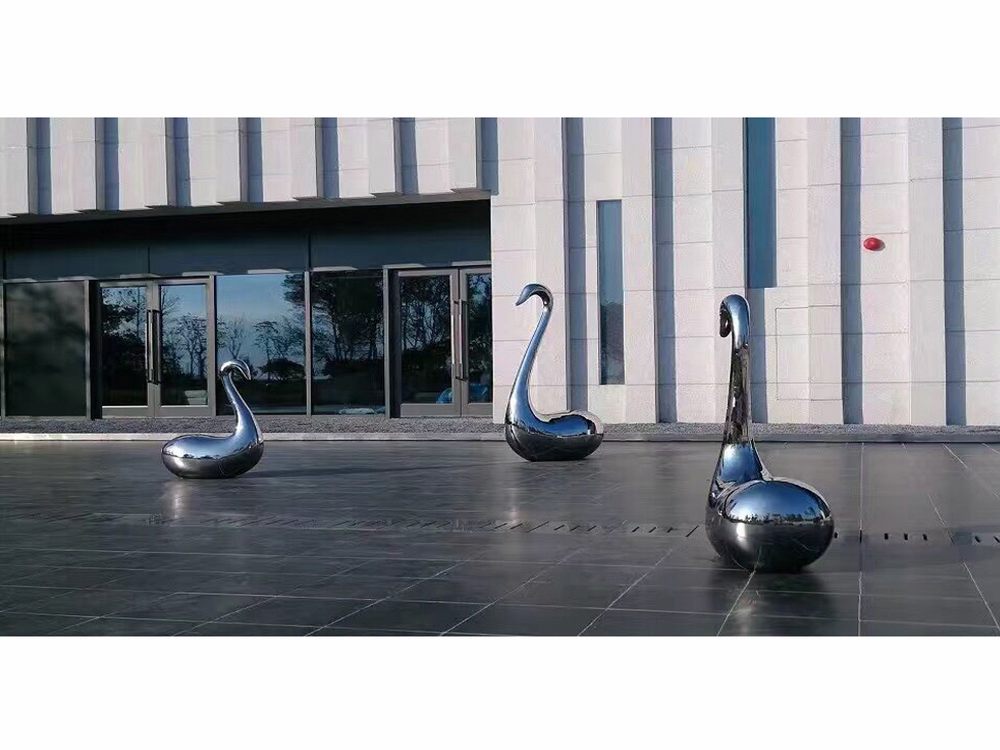
Bronze casting is a revered ancient technique, yet it is prone to several common defects that can compromise quality. Understanding these issues and their solutions is key to producing flawless castings.
1. Porosity – Tiny holes or voids caused by trapped gas or shrinkage during cooling. To avoid this, ensure proper venting in molds and control pouring temperature to minimize gas entrapment.
2. Inclusions – Foreign particles like slag or oxides trapped in the metal. Using clean materials, proper fluxing, and filtering molten bronze can prevent contamination.
3. Cold Shuts – Weak seams where molten metal fails to fuse properly. Maintaining adequate pouring temperature and ensuring smooth metal flow can eliminate this issue.
4. Misruns – Incomplete filling of the mold due to low metal temperature or slow pouring. Preheat molds and optimize gating systems to ensure complete cavity filling.
5. Cracks – Stress fractures from uneven cooling or improper alloy composition. Controlled cooling rates and using the right bronze alloy can mitigate cracking.
By addressing these defects through careful process control, proper mold design, and high-quality materials, foundries can achieve superior bronze castings with minimal flaws. Regular inspections and post-casting treatments like heat treatment further enhance durability and finish.
Mastering these techniques ensures that bronze casting remains a reliable and high-quality manufacturing method for both artistic and industrial applications.