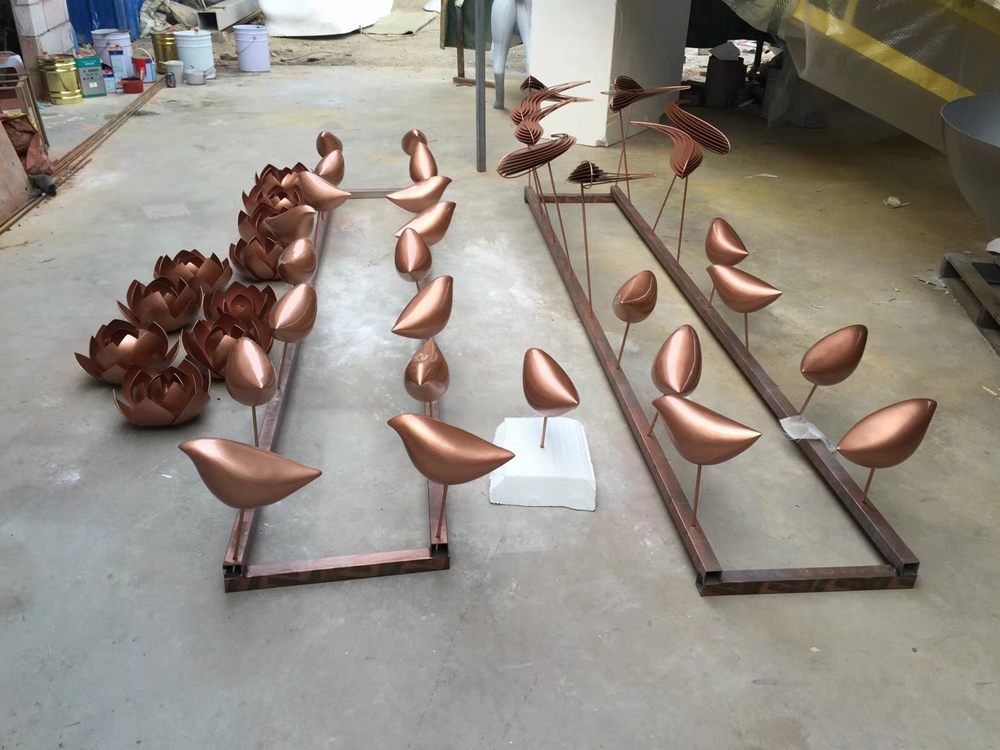
Bronze sculptures have long been admired for their durability and aesthetic appeal, but their weight poses unique challenges for ceiling or wall installations. To address this, sculptors employ several innovative techniques.
One common method is hollow casting, where the bronze is poured into a mold with a ceramic core, creating a lighter final piece without sacrificing structural integrity. Advanced foundries now use precision wax casting techniques to achieve intricate designs with minimal material.
For large installations, sculptors often design segmented pieces that can be assembled on-site. This modular approach allows for easier transportation and reduces stress on mounting structures. Some artists even incorporate internal support frameworks of lighter metals like aluminum or titanium to reinforce thinner bronze sections.
Contemporary sculptors are also experimenting with bronze alloys mixed with lighter metals, maintaining the classic appearance while significantly reducing weight. Computer modeling helps optimize weight distribution before casting begins.
Proper mounting systems are equally crucial. Many installations use aircraft-grade cables or hidden steel brackets engineered to distribute weight across load-bearing walls or ceiling joists. Conservation specialists recommend regular inspections to ensure long-term stability of these gravity-defying artworks.
These solutions demonstrate how technical ingenuity allows bronze sculptures to adorn vertical and overhead spaces while maintaining artistic vision and structural safety.