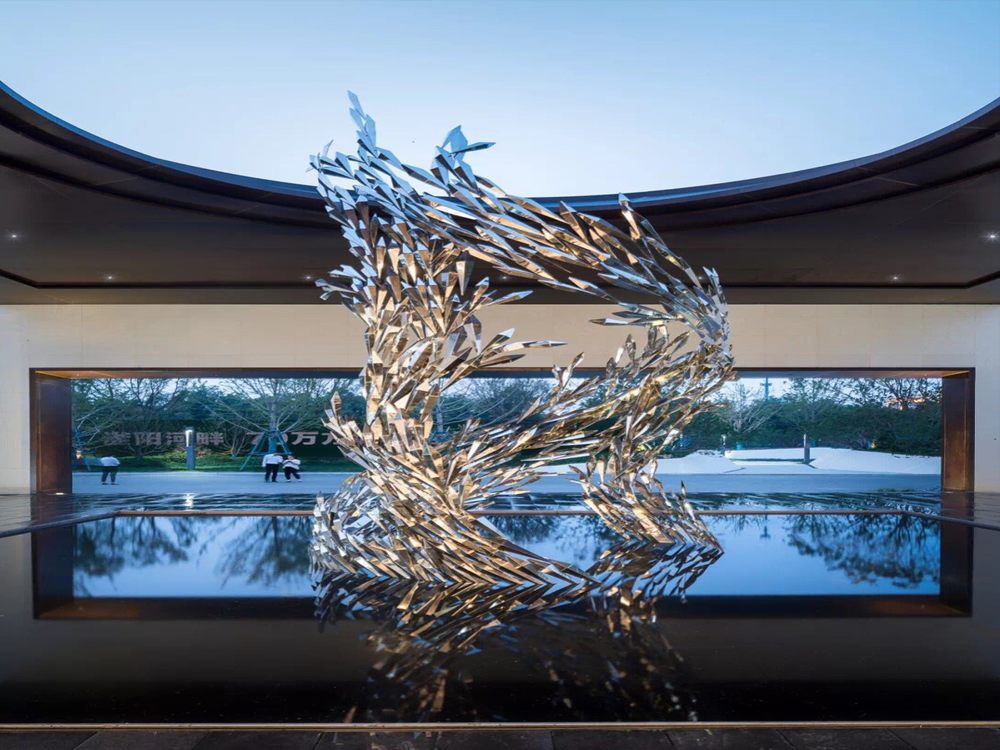
Creating freestanding bronze sculptures without bases is a remarkable feat of artistry and engineering. Sculptors employ several advanced techniques to ensure stability, balancing aesthetics with structural integrity.
One key method involves precise weight distribution. By calculating the sculpture's center of gravity, artists adjust the thickness and density of different sections to prevent tipping. The legs or supporting elements are often reinforced internally with steel armatures, providing hidden strength.
The bronze casting process itself contributes to stability. Hollow casting techniques reduce overall weight while maintaining structural durability. Some sculptors even fill key areas with weighted materials like lead or concrete to lower the center of mass.
Dynamic poses require special consideration. Sculptors may extend limbs or drapery elements to act as counterbalances, creating visual movement while physically anchoring the piece. The base of the sculpture often features subtle flattening or texturing to increase surface friction.
Modern sculptors also utilize computer modeling to test stability before casting, simulating various environmental factors. This combination of traditional craftsmanship and contemporary technology allows for increasingly ambitious freestanding works that defy expectations of balance and form.
Through these methods, bronze sculptures can stand securely without visible supports, maintaining the artist's vision while ensuring public safety and longevity of the artwork. The invisible engineering behind these pieces represents a fascinating intersection of art and science.