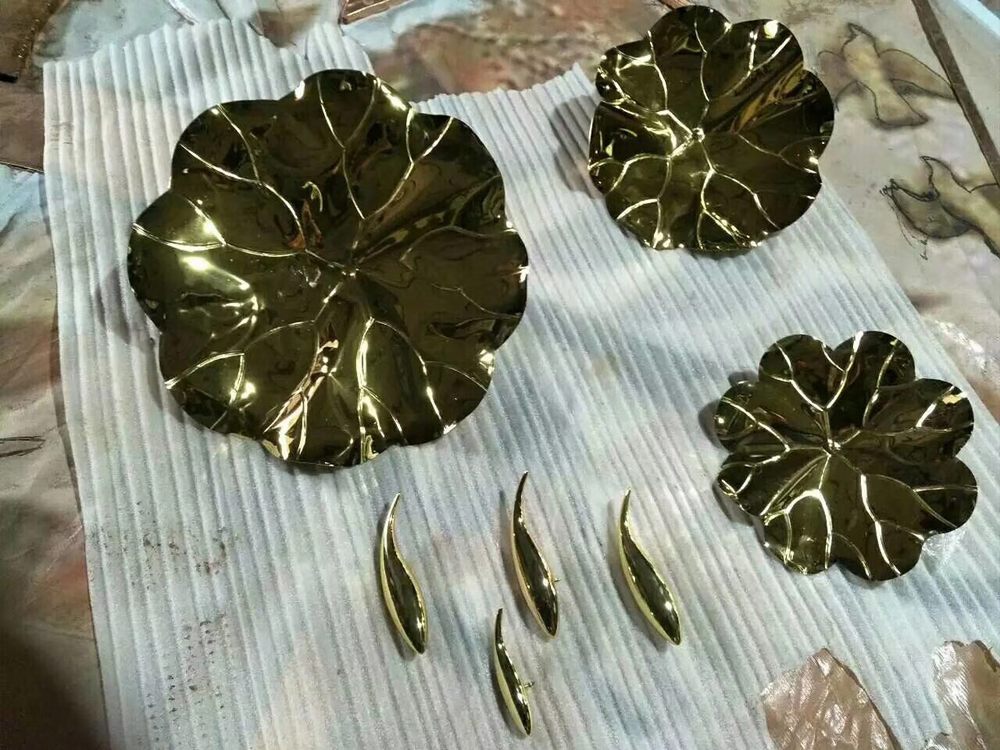
Bronze casting is an ancient art that demands modern precision. Foundries ensure consistency in bronze quality across multiple castings through a combination of meticulous material control, standardized processes, and rigorous testing protocols.
1. Strict Alloy Composition Control
Foundries start by precisely measuring and blending raw materials—copper, tin, and other trace elements—to maintain exact alloy ratios. Spectrometers and X-ray fluorescence analyzers verify chemical composition before pouring, ensuring each batch meets specifications.
2. Standardized Melting and Pouring Procedures
Temperature-controlled furnaces maintain molten bronze within tight thermal ranges (±5°C). Automated pouring systems deliver consistent flow rates, while trained technicians monitor variables like cooling rates to prevent defects like porosity or shrinkage.
3. Process Documentation and Repeatability
Detailed work instructions govern every step—from mold preparation to finishing. Digital tracking systems log parameters for each casting, enabling exact replication of successful batches.
4. Multi-Stage Quality Verification
Each casting undergoes dimensional checks (via CMM machines), mechanical testing (hardness, tensile strength), and visual inspections. Statistical process control charts track variations across production runs.
5. Continuous Improvement Systems
Foundries employ Six Sigma methodologies to analyze defects, with feedback loops adjusting parameters in real-time. Regular alloy sample testing against international standards (e.g., ASTM B584) maintains long-term consistency.
By integrating these practices, modern foundries achieve <2% variance in critical bronze properties—producing castings that meet exacting industrial, artistic, and architectural demands batch after batch.