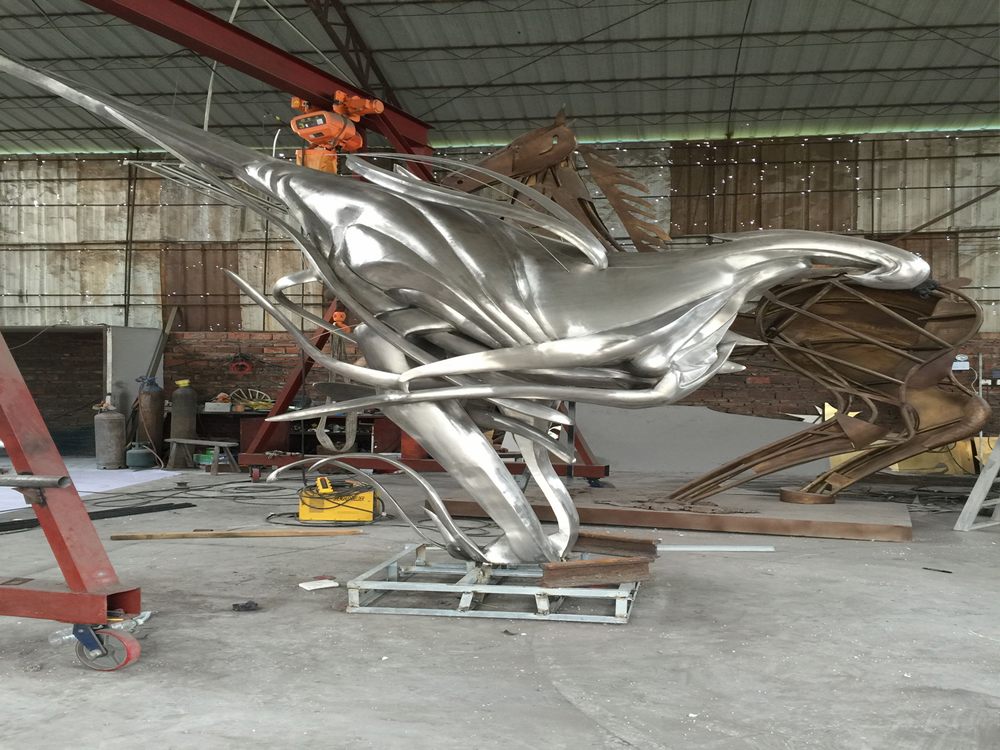
The bronze casting process, while a time-honored technique for creating durable and intricate metal pieces, comes with several significant risks that can compromise quality and safety. Understanding these challenges is crucial for foundries and artisans to ensure successful outcomes.
1. Metal Porosity and Inclusions
Air bubbles or impurities trapped in molten bronze can weaken the final product, leading to cracks or structural failures. Proper degassing and using high-quality alloys minimize this risk.
2. Mold Failure
Cracks or shifts in sand or ceramic molds during pouring can cause misformed castings. Reinforcing molds and controlling pouring temperatures are key preventive measures.
3. Thermal Stress and Cracking
Rapid cooling may induce stress fractures. Controlled cooling rates and post-casting heat treatments help maintain integrity.
4. Toxic Fumes and Burns
Molten bronze releases hazardous fumes, and spills pose severe burn risks. Proper ventilation, PPE, and trained handling are non-negotiable for safety.
5. Dimensional Inaccuracy
Shrinkage or warping during solidification can deviate from design specs. Precision pattern-making and accounting for shrinkage rates are critical.
By addressing these risks through meticulous process control and safety protocols, bronze casters can achieve consistent, high-quality results while protecting their workforce.