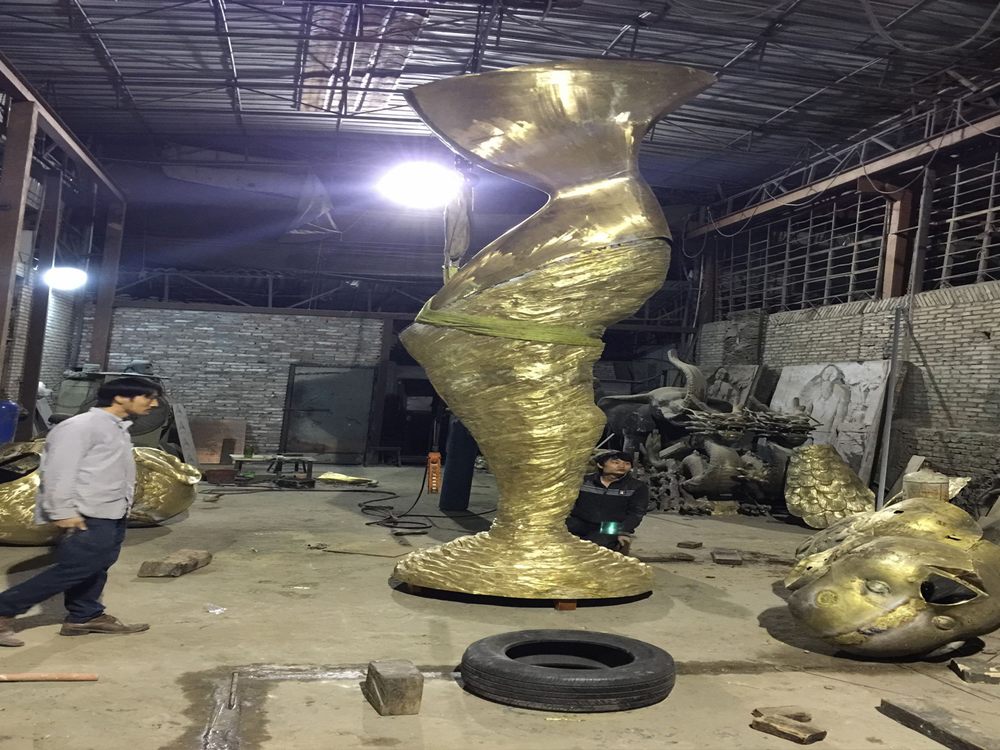
Welding bronze components is a complex yet essential process in metal sculpture, requiring both technical skill and artistic finesse. Sculptors face unique challenges, such as bronze's high thermal conductivity and susceptibility to cracking, but they employ specialized techniques to ensure flawless results.
One common method is TIG (Tungsten Inert Gas) welding, which offers precise control over heat input, minimizing distortion. Sculptors often preheat the bronze to reduce thermal stress and use filler rods with matching alloy compositions to maintain structural integrity. Additionally, post-weld heat treatment helps relieve residual stresses and enhances durability.
To address oxidation, argon or helium shielding gases are used during welding, preventing contamination and ensuring clean joins. For intricate designs, sculptors may opt for brazing or soldering, which require lower temperatures and reduce the risk of damaging delicate details.
Ultimately, mastering bronze welding demands a deep understanding of metallurgy and patience. By combining traditional craftsmanship with modern technology, sculptors transform fragmented bronze pieces into cohesive, enduring works of art.