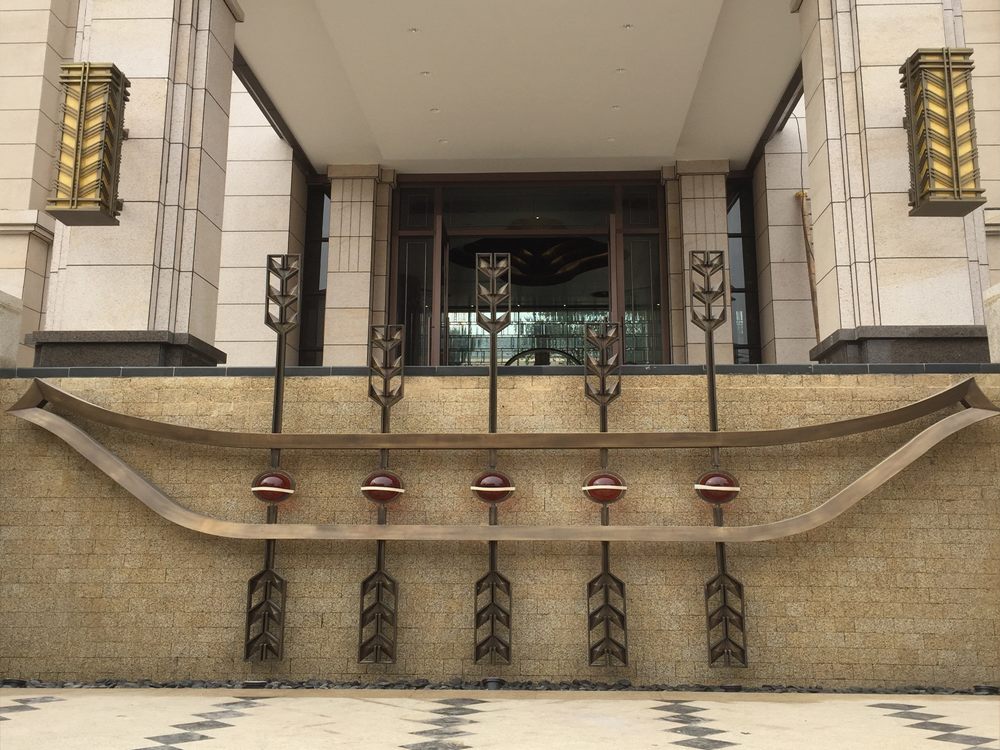
Creating large bronze sculptures from small models is a complex process that demands meticulous planning and technical expertise. Artists face multiple challenges, including maintaining proportions, ensuring structural stability, and preserving intricate details during scaling.
One major hurdle is translating the delicate features of a small model into a massive bronze piece. Artists often use 3D scanning and digital enlargement tools to achieve precision, but manual adjustments remain crucial to retain artistic intent. Structural integrity is another concern—large sculptures require internal armatures or supports to withstand weight and environmental factors.
The casting process itself becomes more demanding at scale. Foundries must carefully manage molten bronze flow to avoid imperfections, while artists oversee patina application to ensure uniform coloration. Collaboration between sculptors, engineers, and foundry technicians is essential throughout this journey from maquette to monument.
Ultimately, successful scaling combines artistic vision with engineering solutions, transforming small inspirations into enduring bronze masterpieces that captivate viewers for generations.