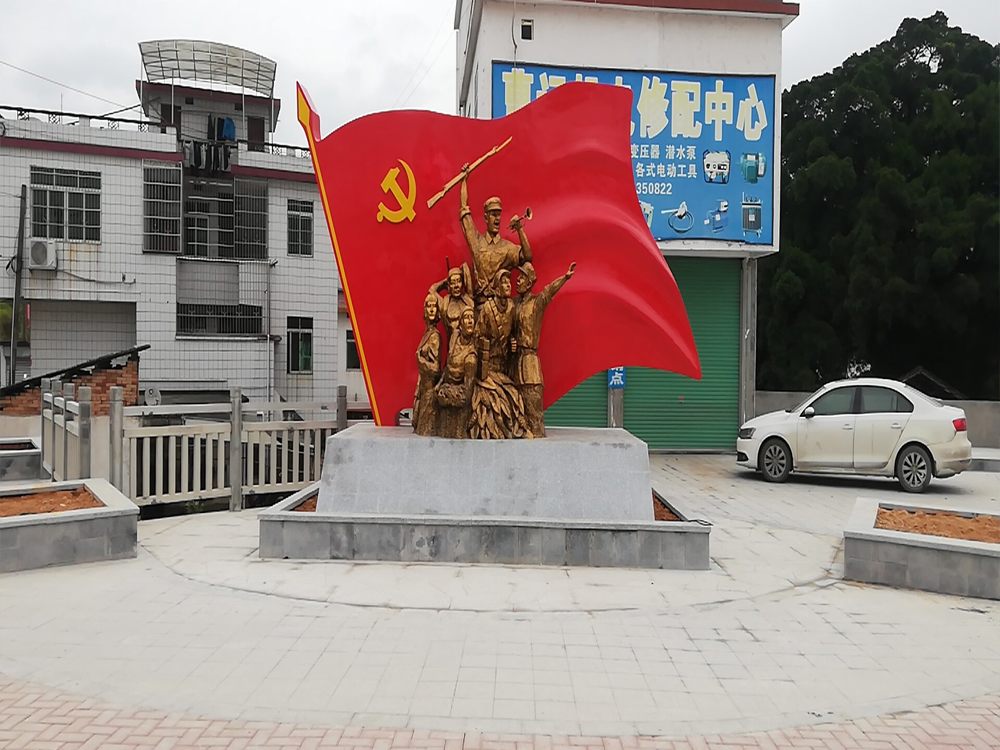
Creating bronze sculptures with hollow interiors is a complex yet fascinating process that combines artistry and metallurgy. The most widely used techniques include the lost wax casting method and sand casting, each offering unique advantages for achieving intricate designs and structural integrity.
1. Lost Wax Casting (Cire Perdue):
This ancient technique involves creating a wax model of the sculpture, coating it with a ceramic shell, and then melting the wax away to leave a hollow mold. Molten bronze is poured into the cavity, resulting in a detailed, lightweight sculpture. Artists often use this method for fine, delicate works due to its precision.
2. Sand Casting:
A more economical approach, sand casting uses compacted sand molds to shape the bronze. The interior is hollowed out by removing a core after casting. While less detailed than lost wax, it’s ideal for larger sculptures and industrial applications.
3. Piece Mold Casting:
Common in traditional Chinese bronze work, this method involves assembling separate mold sections to form a hollow interior. It allows for intricate surface patterns and is reusable for multiple castings.
4. Direct Hollow Construction:
Modern sculptors sometimes weld or assemble pre-cast bronze sheets into hollow forms, offering flexibility in size and design. This technique is popular for contemporary abstract pieces.
Each method balances durability, cost, and artistic expression, making hollow bronze sculptures a timeless medium for sculptors worldwide.