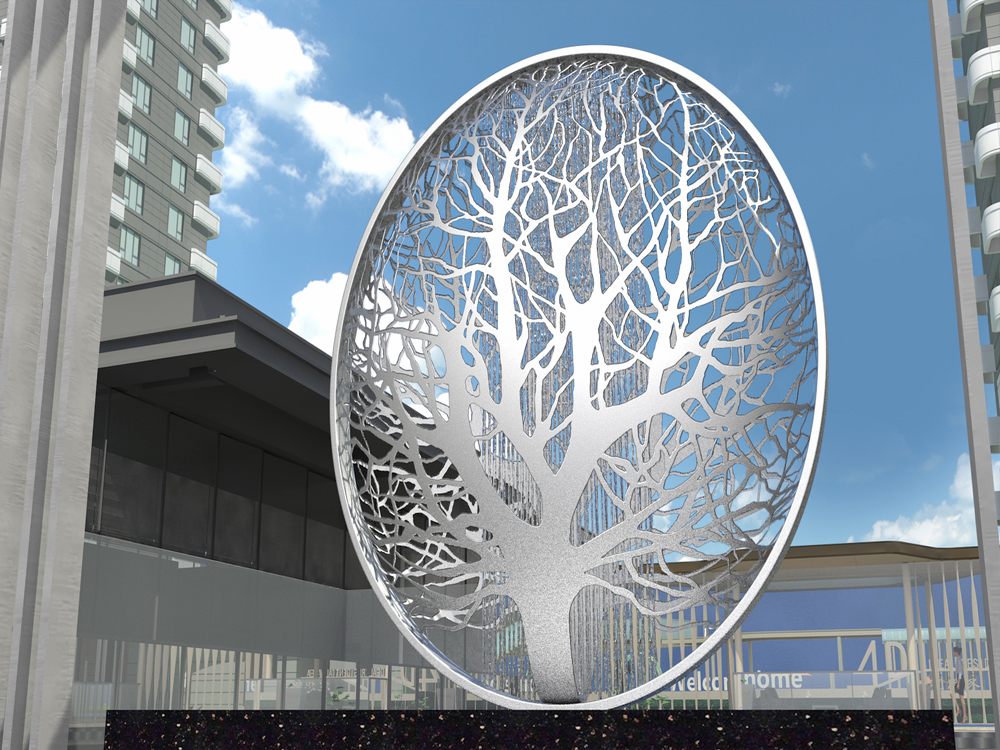
Creating bronze sculptures with thin, extended forms presents unique artistic and technical challenges. One major hurdle is structural integrity—thin bronze sections are prone to warping or breaking during the casting process due to metal shrinkage. Artists must carefully engineer internal armatures or supports to prevent collapse.
The casting process itself becomes more complex with elongated shapes. Molten bronze must flow evenly into narrow cavities, requiring precise temperature control and specialized gating systems. Even slight imperfections can lead to cracks or incomplete pours.
Weight distribution is another critical concern. Extended forms create uneven stress points, demanding meticulous balancing during both creation and installation. Many sculptors use hollow casting techniques to reduce mass while maintaining strength.
Finishing such delicate pieces also proves difficult. Traditional chasing and patination methods must be adapted to avoid damaging thin elements. Artists often develop customized tools and gentler techniques to preserve their fragile creations.
Despite these challenges, the ethereal quality of thin bronze sculptures continues to inspire artists to push material boundaries through innovative engineering and refined craftsmanship.