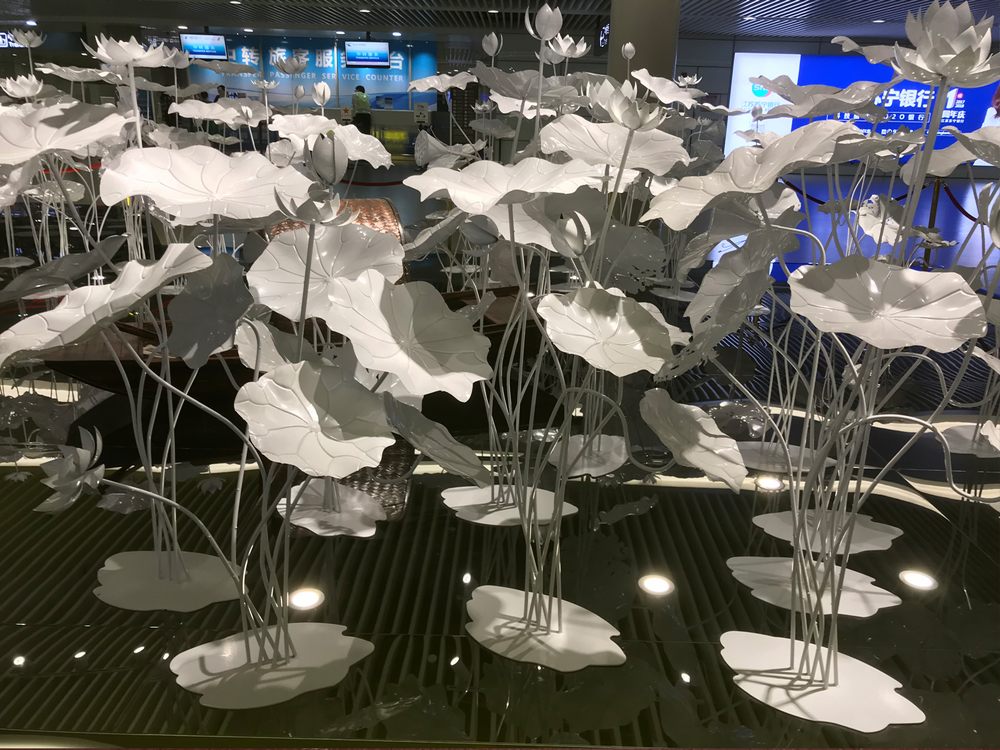
Creating bronze sculptures with intricate internal structures requires a blend of artistry and technical precision. Among the most common techniques, lost-wax casting stands out for its ability to capture fine details. This method involves sculpting a wax model, encasing it in a ceramic mold, and melting the wax away to pour molten bronze into the cavity.
Another popular method is sand casting, where a sand mold is created around a pattern. While less detailed than lost-wax, it’s cost-effective for larger pieces with hollow interiors. For highly complex designs, metal fabrication techniques like welding and assembling pre-cast bronze components are often employed.
Artists may also combine these methods, using 3D-printed cores or internal armatures to support delicate structures. Each technique offers unique advantages, allowing sculptors to balance detail, durability, and scale in their work.