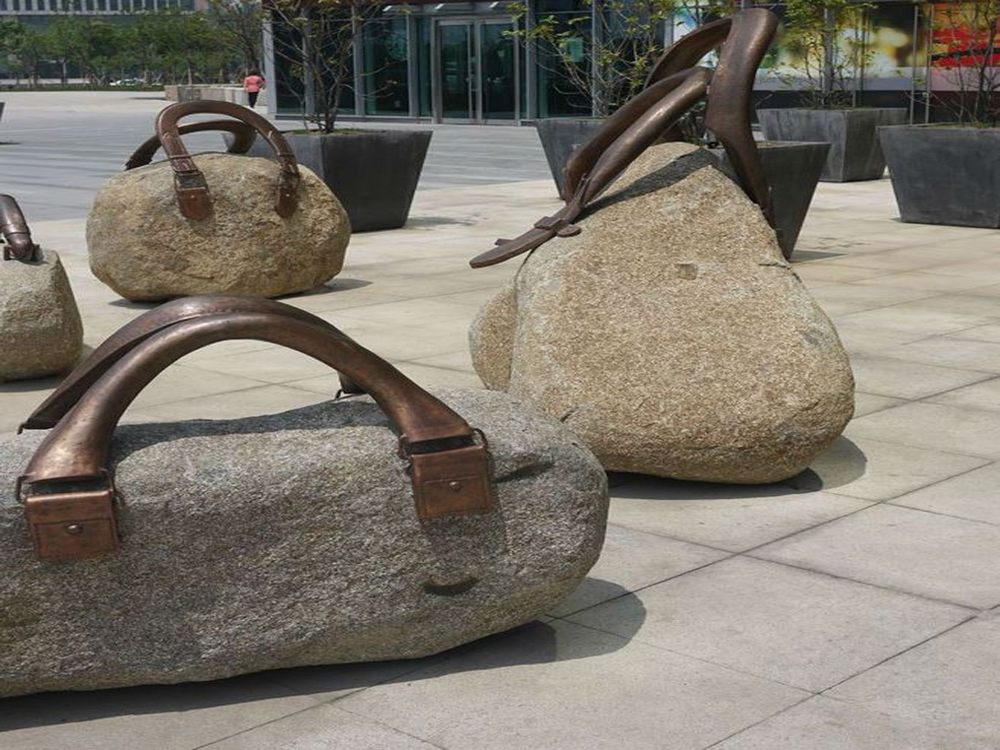
Creating bronze sculptures with complex internal geometries requires specialized techniques to achieve precision and durability. The most common methods include:
1. Lost-Wax Casting: A traditional yet highly detailed process where a wax model is encased in a ceramic shell, melted away, and replaced with molten bronze. This method excels in capturing intricate designs.
2. 3D Printing and Investment Casting: Modern sculptors use 3D printing to create precise wax or resin models, which are then cast using the lost-wax method. This hybrid approach allows for unprecedented complexity.
3. Ceramic Shell Molding: A lightweight alternative to traditional sand casting, this technique involves dipping a wax model in ceramic slurry to form a thin, strong shell capable of fine detail.
4. Sand Casting with Cores: For hollow or multi-chambered sculptures, sand casting with removable cores enables the creation of internal cavities while maintaining structural integrity.
5. Direct Metal Laser Sintering (DMLS): An advanced additive manufacturing technique where bronze powder is fused layer by layer using lasers, ideal for geometries impossible with traditional methods.
Each technique offers unique advantages, blending artistry with engineering to bring intricate bronze sculptures to life.