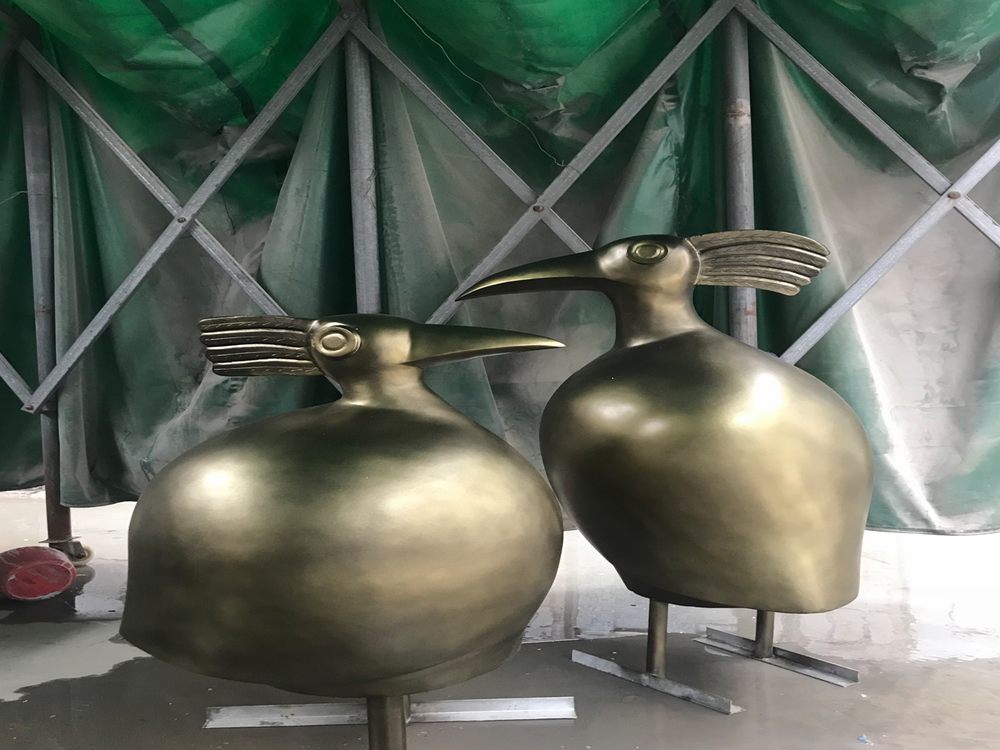
Bronze casting is a meticulous art form where even minor shrinkage during cooling can distort a sculpture’s proportions. To combat this, sculptors employ advanced techniques rooted in centuries of metallurgical knowledge.
The primary method involves the lost wax casting process, where artists first create a wax model slightly larger than the desired final piece. This accounts for the predictable 5-7% shrinkage as molten bronze solidifies. Modern sculptors use digital scaling software to calculate exact expansion ratios based on their specific alloy mixture.
During mold creation, experienced foundries incorporate shrinkage allowances by designing the mold cavity oversized. The gating system (channels for molten metal) is strategically placed to control cooling rates uniformly. Some artists even pre-warp their original designs in anticipation of the metal’s contraction.
Contemporary sculptors often create compensation prototypes – 3D-printed models that simulate the shrinkage effect before final casting. This trial-and-error approach, combined with precise temperature control during cooling, ensures the finished bronze work maintains every intended detail of the artist’s vision.
The most skilled practitioners view shrinkage not as an obstacle, but as a predictable variable in their creative equation – one that separates amateur attempts from museum-quality bronze masterpieces.