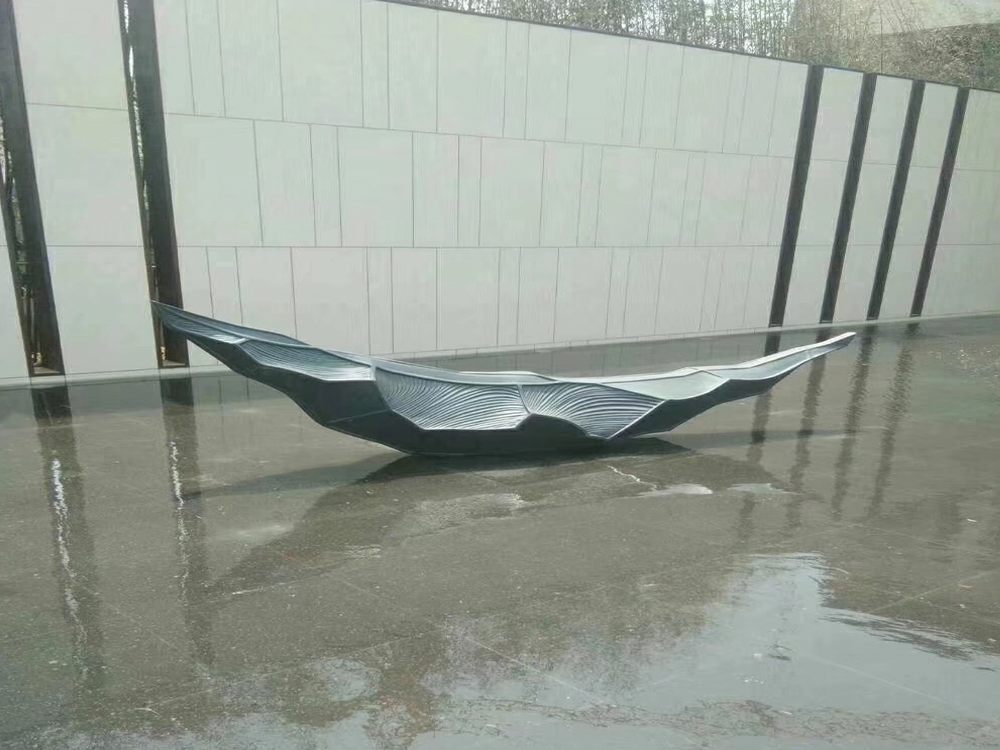
Creating bronze sculptures with intricate details while maintaining structural integrity is a delicate balance of artistry and engineering. Sculptors employ several specialized techniques to accomplish this feat.
The most common method is the lost wax casting process, which allows for exceptional precision. Artists first sculpt the fine details in wax, which is then coated in a ceramic shell. When molten bronze replaces the wax, it captures every minute detail of the original wax model. This technique preserves even the most delicate features while producing a durable metal form.
Material science plays a crucial role in maintaining strength. Modern bronze alloys, typically composed of 90-95% copper with tin and other metals, offer both workability for fine details and structural stability. The thickness of the bronze casting is carefully calculated - thinner in detailed areas but reinforced in structural sections.
Many sculptors use a technique called "chasing" to refine details after casting. This involves carefully hammering and tooling the metal surface to enhance textures and sharpen features without weakening the overall structure.
Advanced patination methods further highlight details through controlled chemical reactions that create color variations in recessed areas, making intricate patterns visually pop while the underlying metal remains strong.
The combination of these techniques allows sculptors to create breathtakingly detailed bronze works that can withstand centuries of display, proving that artistry and durability can coexist in metal sculpture.