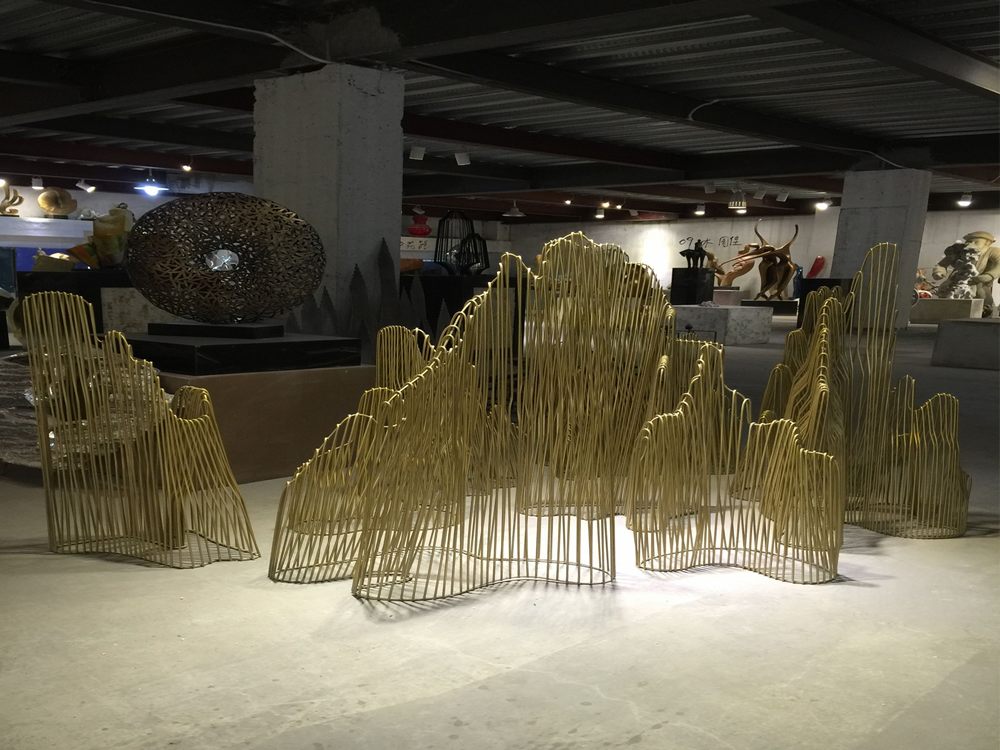
Bronze casting is a complex process that often encounters defects, impacting the quality and durability of the final product. The most common defects include porosity, shrinkage cavities, cold shuts, misruns, and inclusions.
1. Porosity: Caused by trapped gas or improper venting, porosity weakens the casting. Mitigation involves proper mold venting, controlled pouring temperatures, and degassing the molten bronze.
2. Shrinkage Cavities: These occur when molten metal contracts unevenly during cooling. Using chills, risers, and optimized gating systems helps distribute heat evenly and minimize shrinkage.
3. Cold Shuts and Misruns: Incomplete filling of the mold results in weak seams or incomplete sections. Increasing pouring temperature, improving fluidity, and ensuring proper mold design can prevent these issues.
4. Inclusions: Foreign particles like slag or oxides weaken the casting. Proper fluxing, filtration, and careful handling of molten metal reduce contamination.
By understanding these defects and applying corrective measures, foundries can enhance casting quality and reduce waste. Regular inspection and process optimization are key to minimizing defects in bronze casting.