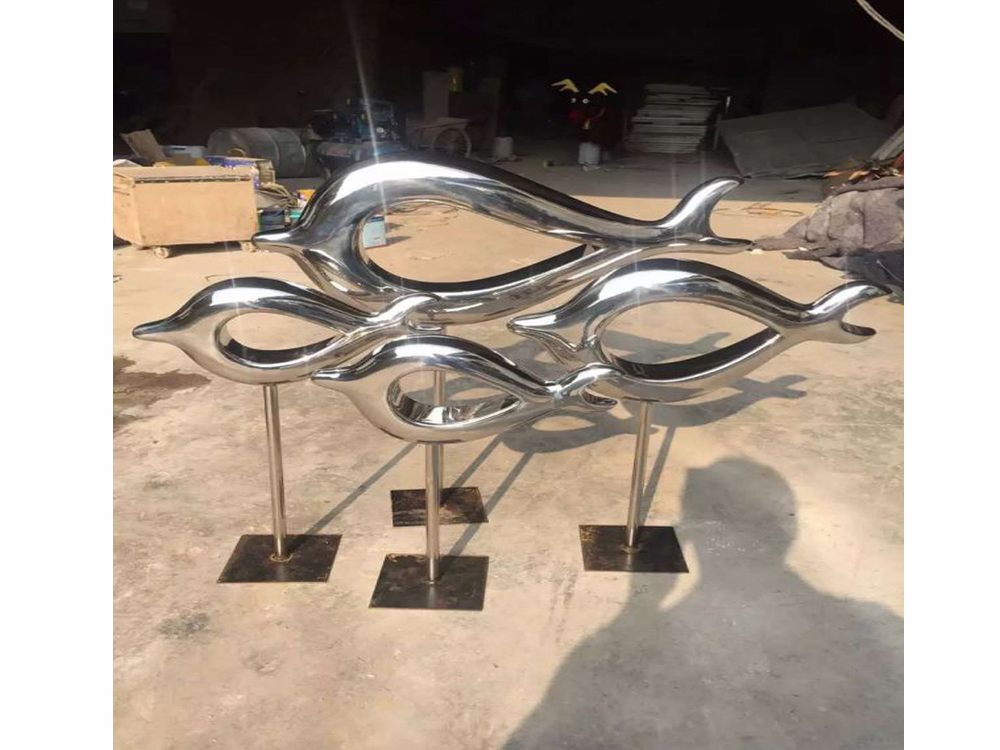
In the intricate world of lost-wax casting (also called investment casting), wax quality serves as the unsung hero determining final product excellence. The wax pattern forms the very foundation of this ancient yet precise metal-forming technique, with its characteristics directly influencing every subsequent stage.
High-quality casting wax exhibits three crucial properties: appropriate viscosity for detail reproduction, thermal stability to prevent distortion, and complete burnout characteristics. When these parameters are optimized, the wax pattern captures microscopic details from the master mold that will later translate into flawless metal surfaces.
The wax's composition significantly affects casting outcomes. Premium blends maintain dimensional stability during handling and resist cracking under temperature fluctuations. Inferior waxes often cause surface imperfections in final castings, as incomplete burnout leaves residues that disrupt metal flow. Modern formulations may incorporate polymer additives to enhance strength while maintaining clean decomposition properties.
Wax quality also determines economic efficiency in production. Consistent wax properties reduce rejection rates by minimizing common defects like veining or misruns. Furthermore, specialized waxes enable specific applications - flexible waxes for undercut designs or water-soluble variants for complex cores.
As additive manufacturing integrates with traditional lost-wax processes, wax quality requirements evolve. 3D-printed wax patterns must meet the same stringent standards as conventionally molded ones, proving that regardless of pattern creation method, wax quality remains the linchpin of casting success.