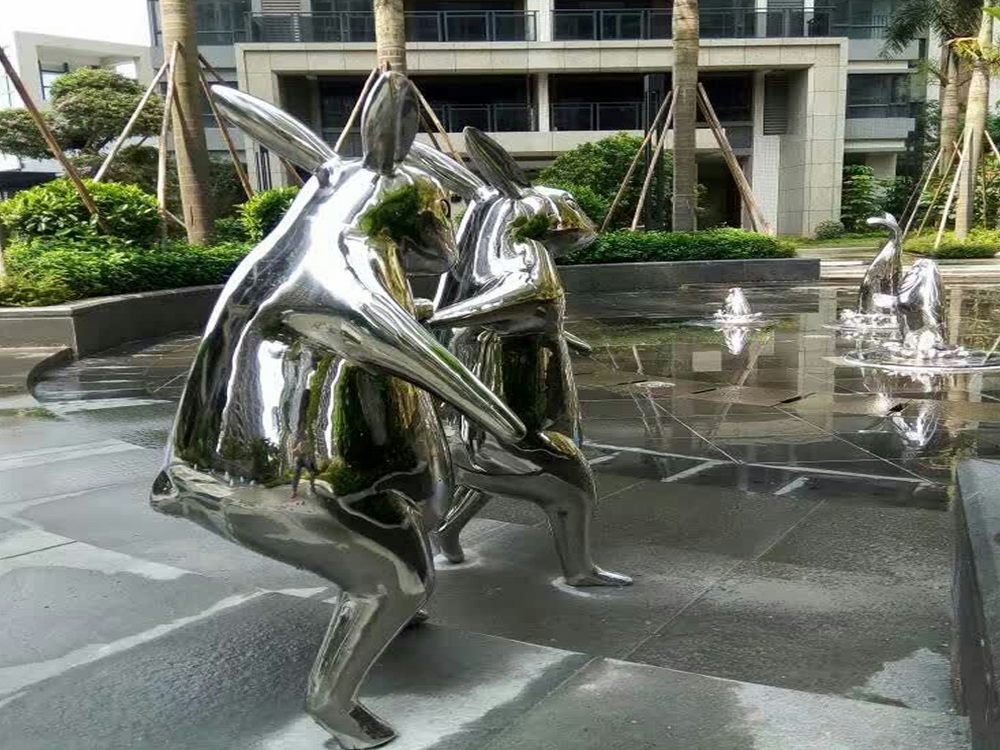
Creating a seamless join between multiple bronze cast pieces is a meticulous process that combines artistry and technical skill. Sculptors begin by carefully designing the sculpture in sections that account for casting limitations. After the individual bronze pieces are cast using the lost-wax method, artisans employ several specialized techniques to achieve invisible joins.
The primary method involves precise metal welding, where sculptors use TIG or MIG welding to fuse sections together. This requires exceptional control to match the bronze's thickness and composition. Following welding, the chasing process begins – craftsmen painstakingly file, grind, and polish the welded areas to eliminate any visible seams.
For particularly complex joins, sculptors may use mechanical fasteners like dowels or pins combined with welding for added strength. The final magic happens during patination, where chemical treatments and heat application create uniform coloration across the entire sculpture, effectively disguising any remaining join lines.
Modern sculptors also utilize advanced techniques like laser scanning and 3D modeling to perfect join alignment before casting. The result is a breathtaking bronze sculpture where the artist's hand becomes invisible, leaving only the unified artistic vision apparent to the viewer.