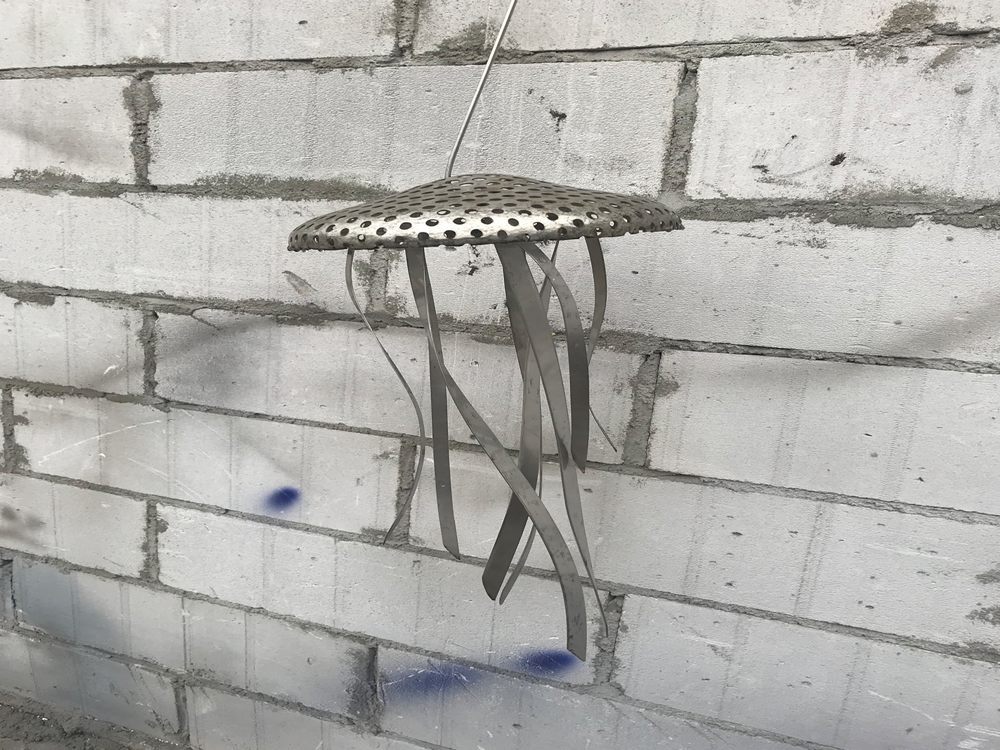
Bronze sculptures that incorporate water or other liquids are a mesmerizing fusion of art and engineering. Artists achieve this effect through a combination of traditional metal casting techniques and innovative design.
The process begins with a detailed clay or wax model, which is used to create a mold for bronze casting. To integrate water, artists carefully plan the sculpture's structure, ensuring hollow channels or reservoirs are embedded during casting. Modern techniques like 3D modeling help visualize liquid flow patterns before fabrication.
For dynamic water features, pumps and tubing systems are concealed within the bronze framework. The metal's natural corrosion resistance makes it ideal for water contact, though artists often apply protective patinas. Some creators experiment with other liquids like oil or colored solutions, using transparent acrylic elements to contain them while maintaining the bronze aesthetic.
Advanced methods include electroforming - building up bronze layers around temporary water channels - or combining bronze with glass components. The result is living art where flowing liquids interact with the metal's surface, creating ever-changing reflections and movement.
These sculptures require collaboration between artists, foundries, and engineers to solve technical challenges like pressure regulation and material compatibility. The finished pieces transform public spaces and galleries with their kinetic beauty, demonstrating bronze's versatility beyond static forms.
Maintenance considerations include water treatment to prevent mineral buildup and periodic waxing of bronze surfaces. As technology advances, artists continue pushing boundaries with interactive liquid-bronze installations that respond to viewers or environmental conditions.