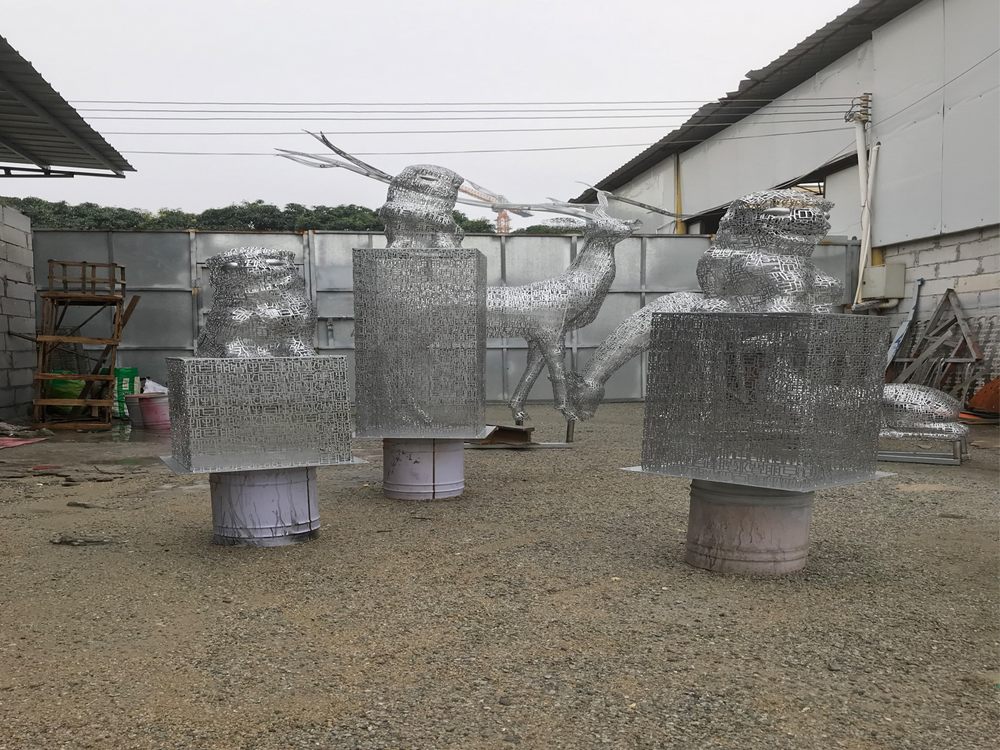
Creating bronze sculptures with deep recesses presents unique challenges for sculptors, requiring specialized techniques to achieve intricate details and durability. One of the most common methods is the lost wax casting process, which allows artists to capture even the most delicate features.
Sculptors begin by crafting a detailed clay or wax model, carefully shaping the deep recesses to ensure they are preserved during casting. The model is then encased in a ceramic mold, and molten bronze is poured into the cavity once the wax is melted away. This method ensures precision, as the bronze fills every crevice of the original design.
To enhance durability, sculptors often use reinforcements like internal armatures or thicker metal layers in vulnerable areas. Post-casting, meticulous chasing and patination bring out the sculpture's textures and depths, highlighting the recesses with contrasting finishes.
Innovations like 3D printing and digital modeling now complement traditional techniques, enabling even greater complexity in bronze sculptures. By combining time-honored craftsmanship with modern tools, sculptors continue to push the boundaries of metal art, creating stunning works with profound depth and detail.