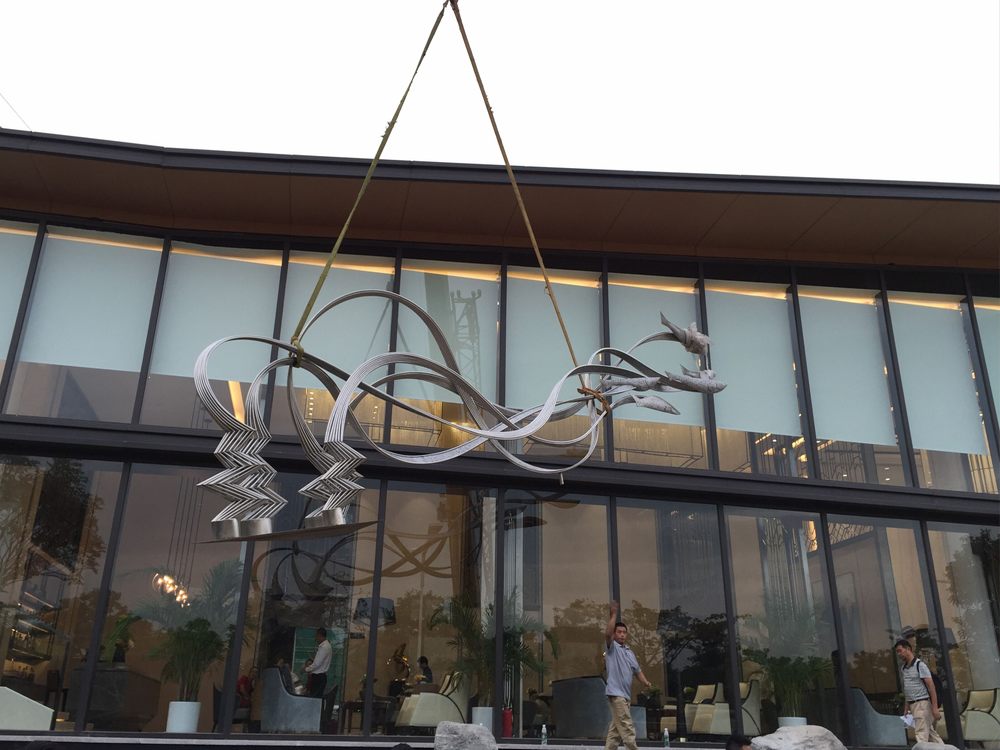
Bronze casting is an ancient art form that has evolved significantly over centuries. The choice of mold type—traditional or experimental—plays a crucial role in the final artwork's quality and characteristics.
Traditional bronze casting molds typically use time-tested materials like clay, sand, or plaster. These methods, such as the lost-wax technique, prioritize precision and durability. The process involves creating a wax model, coating it with refractory material, and then melting the wax away to leave a cavity for molten bronze. Traditional molds excel at producing detailed, consistent results favored for classical sculptures and functional items.
Experimental molds, by contrast, embrace modern materials and unconventional approaches. Artists might incorporate 3D-printed components, silicone rubber, or even organic materials. These innovative molds allow for greater artistic freedom, enabling unique textures, asymmetrical forms, and abstract designs impossible with traditional methods. The experimental approach often yields one-of-a-kind pieces but may sacrifice some structural integrity.
Key differences include:
1. Material versatility (limited in traditional vs expansive in experimental)
2. Production time (weeks/months for traditional vs potentially faster experimental processes)
3. Surface finish (smoother traditional results vs intentionally textured experimental pieces)
4. Cost considerations (generally higher for experimental due to specialized materials)
5. Artistic control (precision in traditional vs spontaneity in experimental)
Contemporary artists frequently blend both approaches, using traditional methods for structural elements while incorporating experimental touches for artistic expression. The mold choice ultimately depends on the desired aesthetic, functional requirements, and the artist's creative vision. As bronze casting continues evolving, the boundary between traditional and experimental techniques becomes increasingly fluid.