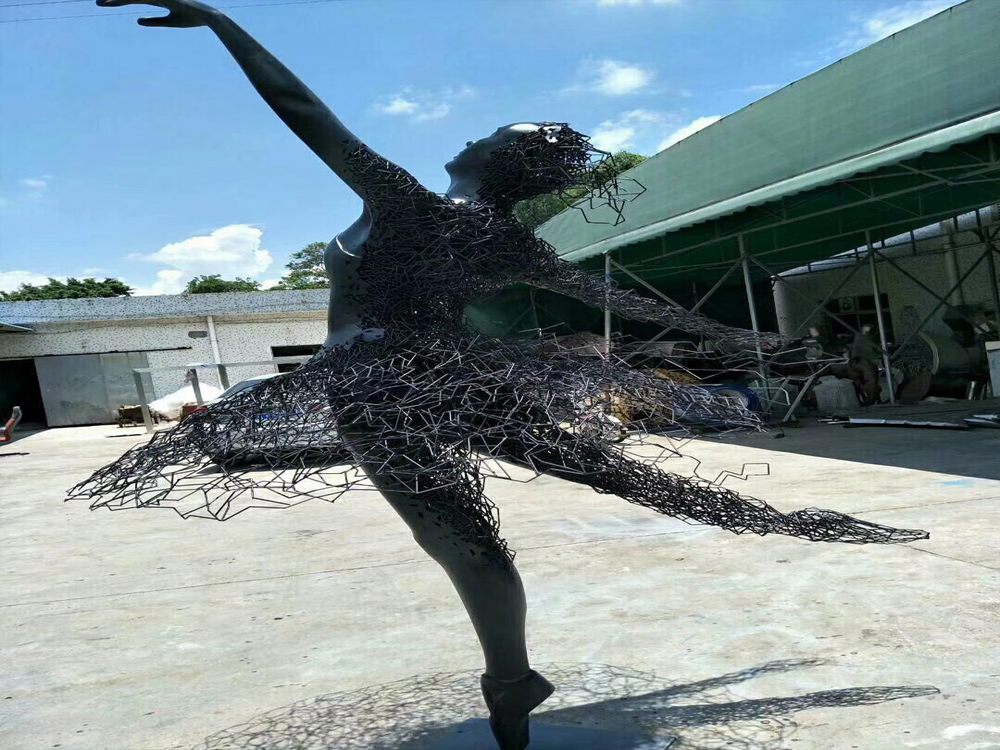
Alloy separation in antique bronze sculptures is a frequent issue that compromises their structural integrity and aesthetic value. One primary cause is corrosion, where chemical reactions between the bronze alloy (typically copper and tin) and environmental elements like moisture, salt, or pollutants lead to weakening and flaking. Over time, differential corrosion can occur, where one metal in the alloy degrades faster than another, causing separation.
Another significant factor is thermal stress. Bronze expands and contracts with temperature fluctuations, and repeated cycles can create micro-cracks, eventually causing the alloy components to separate. This is especially common in sculptures exposed to outdoor conditions.
Improper restoration techniques also contribute to alloy separation. Harsh cleaning methods or incompatible repair materials can accelerate degradation. Additionally, inherent flaws in the original casting, such as uneven alloy mixing or trapped gases, may lead to long-term instability.
Lastly, mechanical wear from handling or environmental abrasion can exacerbate existing weaknesses. Preserving these artworks requires controlled environments, gentle cleaning, and expert conservation to mitigate alloy separation risks. Understanding these causes helps collectors and conservators protect these historical treasures.