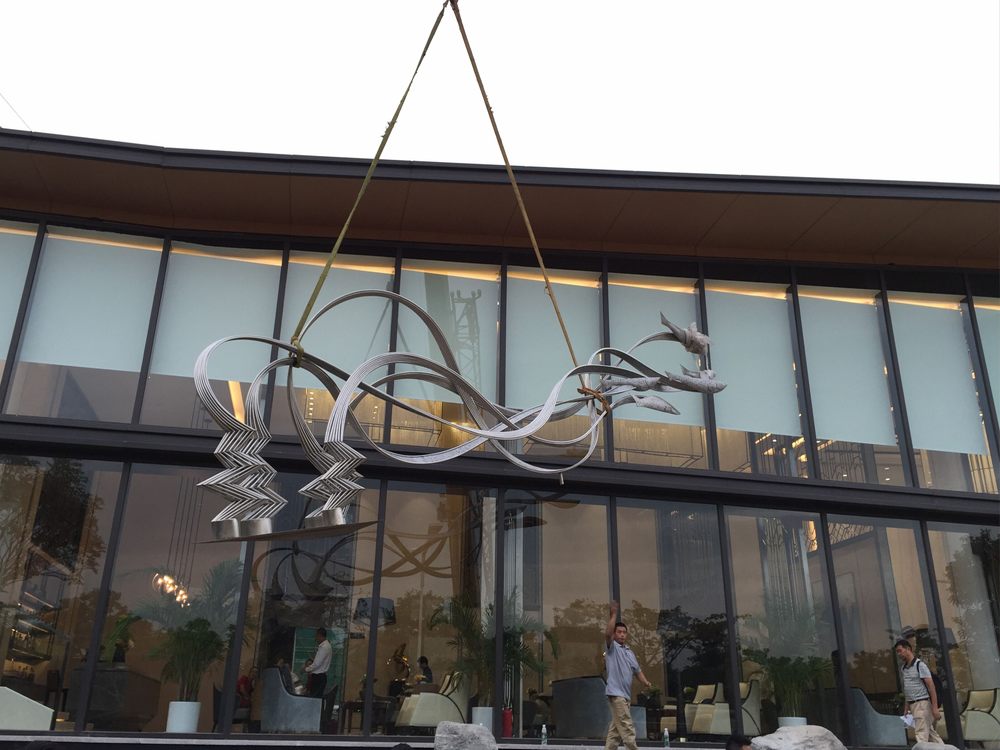
Alloy segregation in large bronze castings is a critical metallurgical issue that can compromise the structural integrity and performance of the final product. The most common causes include uneven cooling rates, which lead to differential solidification and concentration gradients. Improper alloy composition, such as excessive zinc or tin, can also promote segregation by altering the melting and solidification behavior. Additionally, inadequate stirring or insufficient homogenization during the molten phase often results in localized variations in alloy distribution. The size and geometry of large castings exacerbate these issues, as thicker sections cool slower, creating pockets of segregated material. Finally, impurities or inclusions can act as nucleation sites, further disrupting uniform alloy distribution. Addressing these factors through controlled cooling, precise alloy formulation, and thorough mixing is essential to minimize segregation defects.