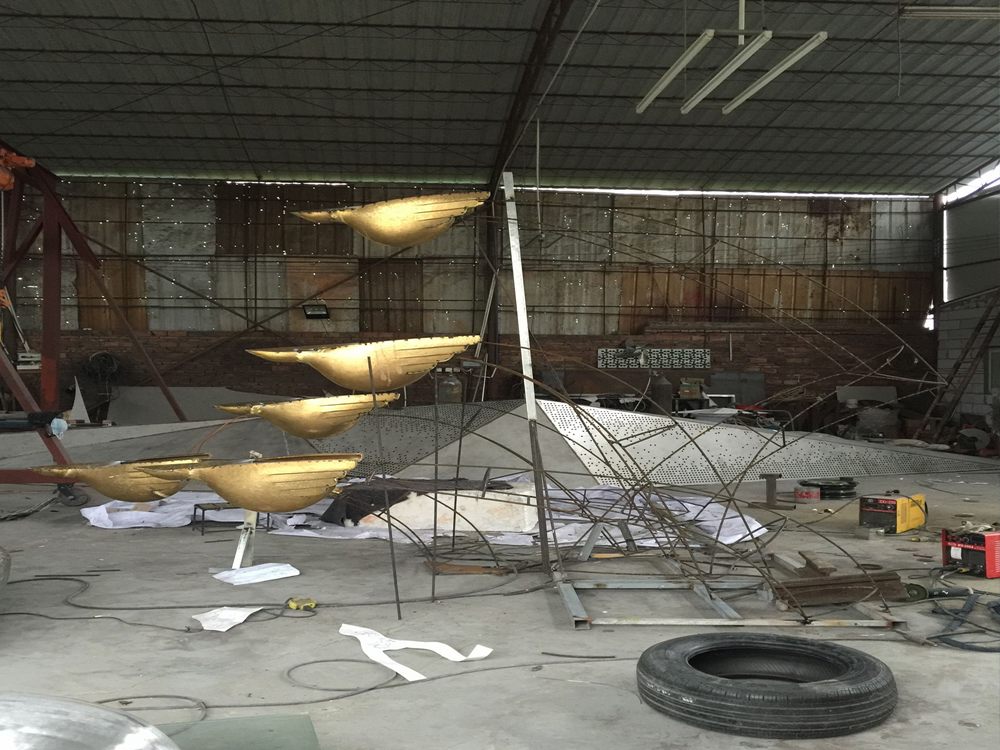
Creating bronze sculptures with translucent or hollow elements presents unique artistic and technical challenges. One of the primary difficulties lies in the casting process itself. Bronze, a dense and heavy alloy, requires precise control to achieve thin, translucent sections without compromising structural integrity. Traditional lost-wax casting methods must be adapted to accommodate these delicate features, often demanding specialized molds and cooling techniques to prevent warping or cracking.
Hollow elements introduce additional complexities, as uneven wall thickness can lead to weak points or distortions during cooling. Artists must carefully balance aesthetics with durability, ensuring the sculpture can withstand environmental factors like temperature changes and physical stress. The interplay of light and shadow in translucent bronze adds another layer of difficulty, requiring meticulous surface finishing to achieve the desired visual effect.
Material limitations also play a role. Achieving translucency in bronze often involves alloy adjustments or post-casting treatments, which can alter the metal's properties. Finally, the cost and expertise required for such specialized work make these sculptures rare and highly sought after in the art world. Mastering these challenges, however, results in breathtaking pieces that push the boundaries of traditional bronze artistry.