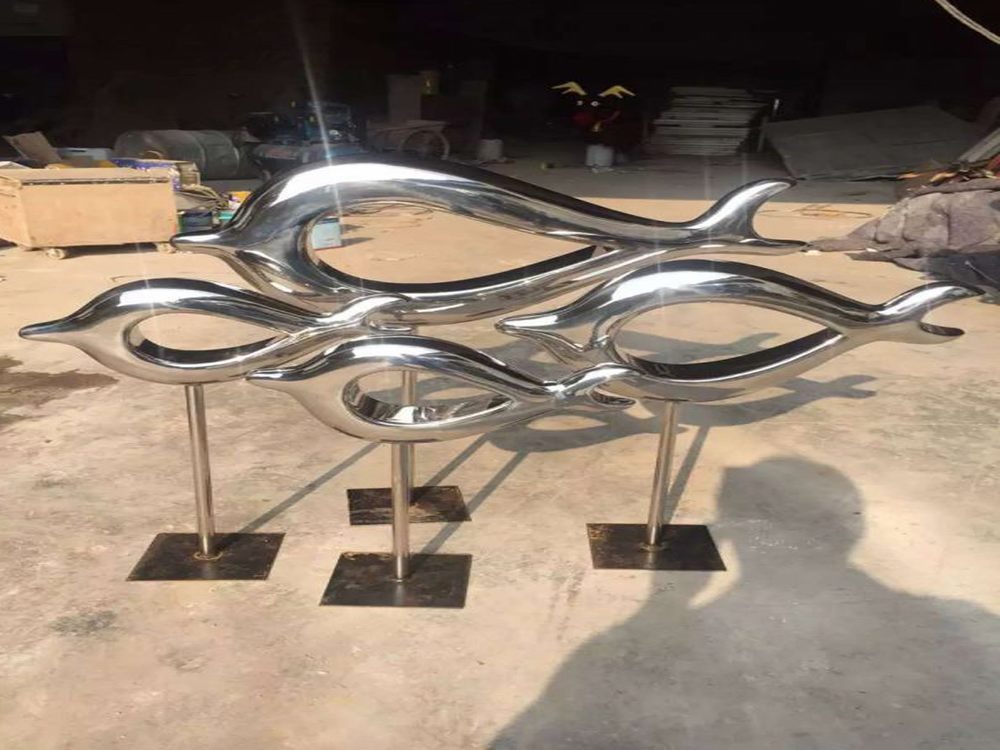
The lost-wax casting process, an ancient yet highly refined technique, plays a pivotal role in determining the final texture and detail of bronze sculptures. By meticulously crafting a wax model, artists can achieve unparalleled precision in their designs. Once the wax is encased in a ceramic mold and melted away, molten bronze is poured into the cavity, capturing even the most delicate features of the original wax model.
This method allows for intricate details, such as fine lines, subtle curves, and lifelike textures, to be preserved with remarkable fidelity. Unlike other casting techniques, lost-wax casting minimizes air bubbles and imperfections, resulting in a smoother, more refined surface. Additionally, the flexibility of wax enables artists to experiment with complex forms that would be difficult to replicate through direct carving or machining.
The final texture of the bronze sculpture is further enhanced through post-casting processes like chasing and patination. Chasing involves refining the metal surface to remove any residual flaws, while patination adds color and depth, accentuating the sculpture’s details.
Ultimately, the lost-wax casting process not only preserves the artist’s original vision but also elevates the tactile and visual qualities of bronze sculptures, making it a cornerstone of fine metal artistry.