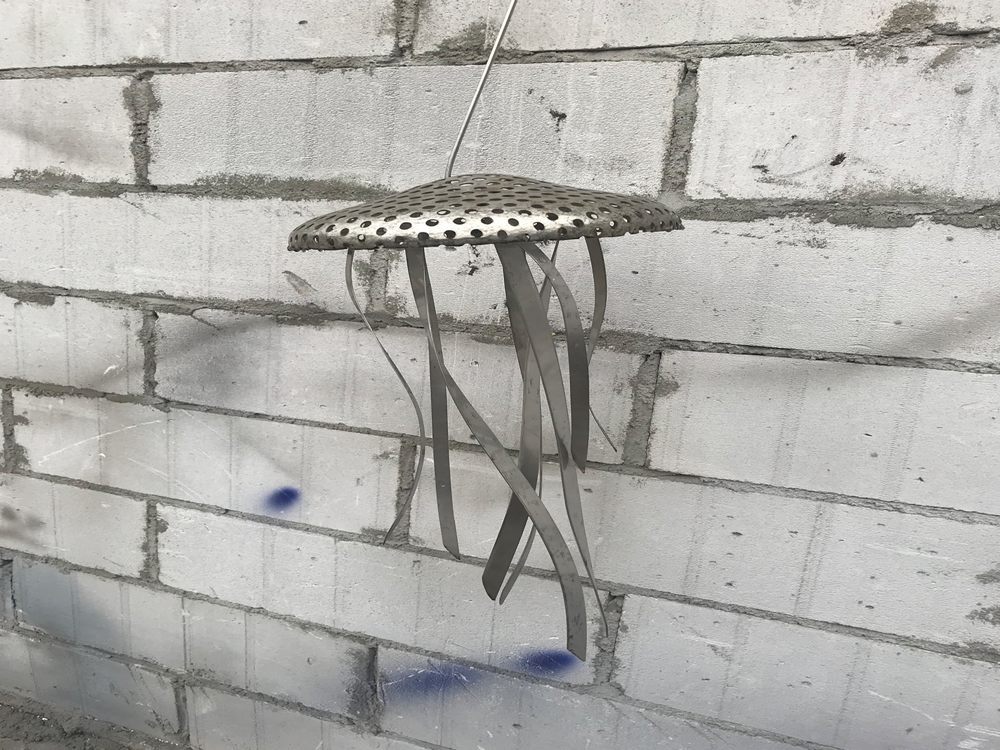
Bronze casting is a complex process that often encounters defects, impacting the quality and durability of the final product. The most common defects include porosity, shrinkage cavities, misruns, cold shuts, and inclusions.
Porosity occurs due to trapped gases or improper venting, leading to weak spots. To mitigate this, ensure proper mold drying, use degassing agents, and optimize pouring temperature.
Shrinkage cavities form when molten bronze contracts unevenly during cooling. Solutions include designing adequate risers and modifying the gating system to promote directional solidification.
Misruns and cold shuts result from incomplete filling of the mold, often due to low pouring temperature or slow flow. Increasing metal fluidity and preheating molds can prevent these issues.
Inclusions (foreign particles) are avoided by maintaining clean melting practices and using filters in the gating system.
Implementing strict quality control measures, such as non-destructive testing and process monitoring, significantly reduces defects, ensuring high-quality bronze castings.