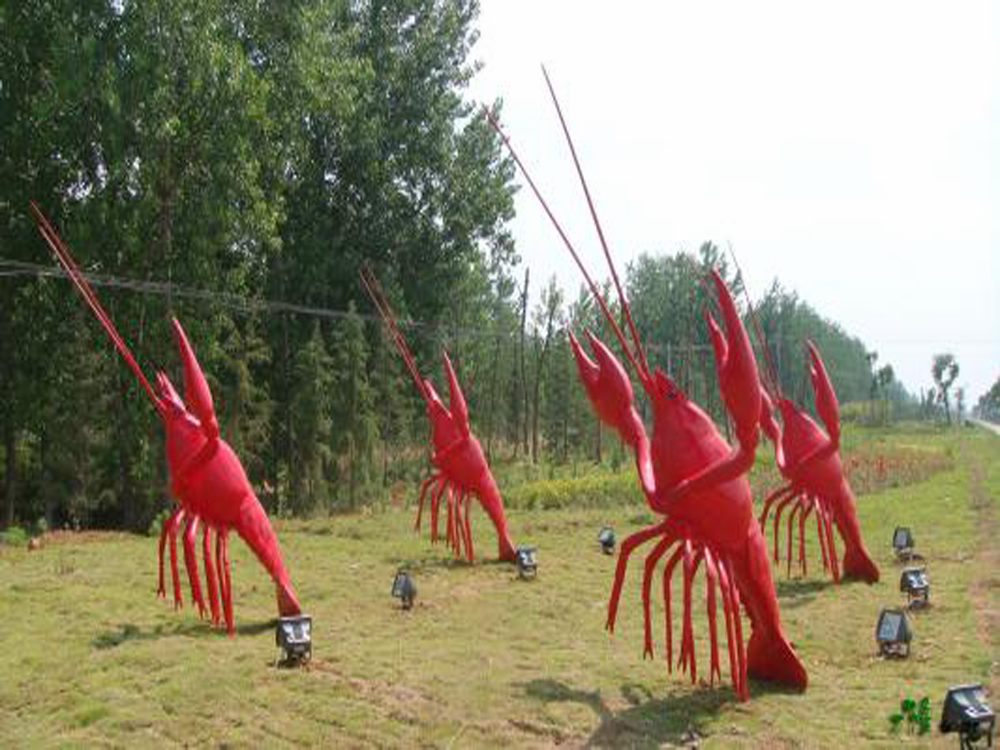
Creating bronze sculptures with movable parts or joints presents a unique set of challenges that blend artistry with engineering. One major hurdle is the material itself—bronze, while durable, is less flexible than other metals, making it prone to cracking or breaking at stress points. Artists must carefully design joints to allow movement without compromising structural integrity, often requiring precise calculations and prototyping.
Another challenge lies in the casting process. Traditional lost-wax casting can complicate the creation of interlocking or rotating parts, demanding meticulous mold-making and post-casting adjustments. Additionally, friction and wear over time can degrade movable components, necessitating innovative solutions like hidden bearings or lubrication systems.
Balancing aesthetics with functionality is also critical. Movable joints must blend seamlessly into the sculpture’s design, avoiding an overly mechanical appearance. This often requires iterative testing and collaboration between sculptors and engineers. Despite these obstacles, the result—a dynamic, interactive bronze sculpture—can be a breathtaking fusion of art and ingenuity.