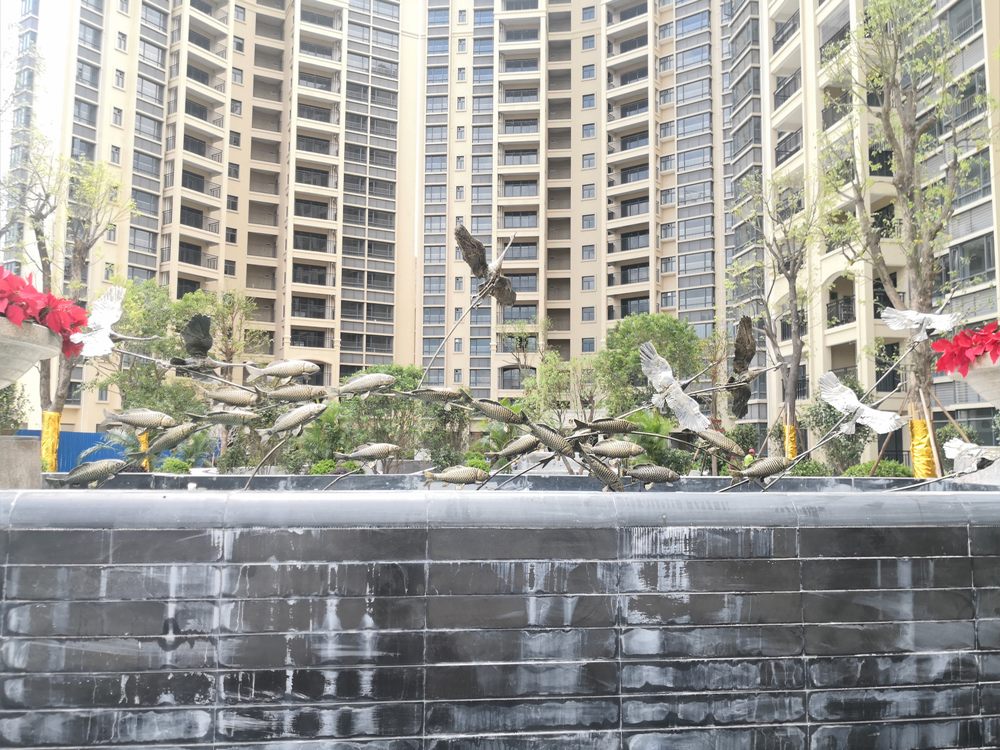
Bronze casting is a revered ancient art, but even skilled artisans encounter defects. The most common flaws include porosity, shrinkage cavities, cold shuts, and misruns. Porosity occurs when gas bubbles become trapped, creating weak spots—addressed by proper venting and degassing molten bronze. Shrinkage cavities form during cooling; controlled cooling rates and strategic riser placement prevent this. Cold shuts (incomplete fusion) and misruns (incomplete filling) stem from low metal temperature or slow pouring—solved by preheating molds and optimizing flow. Modern techniques like X-ray inspection detect hidden flaws, while traditional methods like chasing and welding repair surface imperfections. Understanding these challenges ensures durable, high-quality bronze artworks.