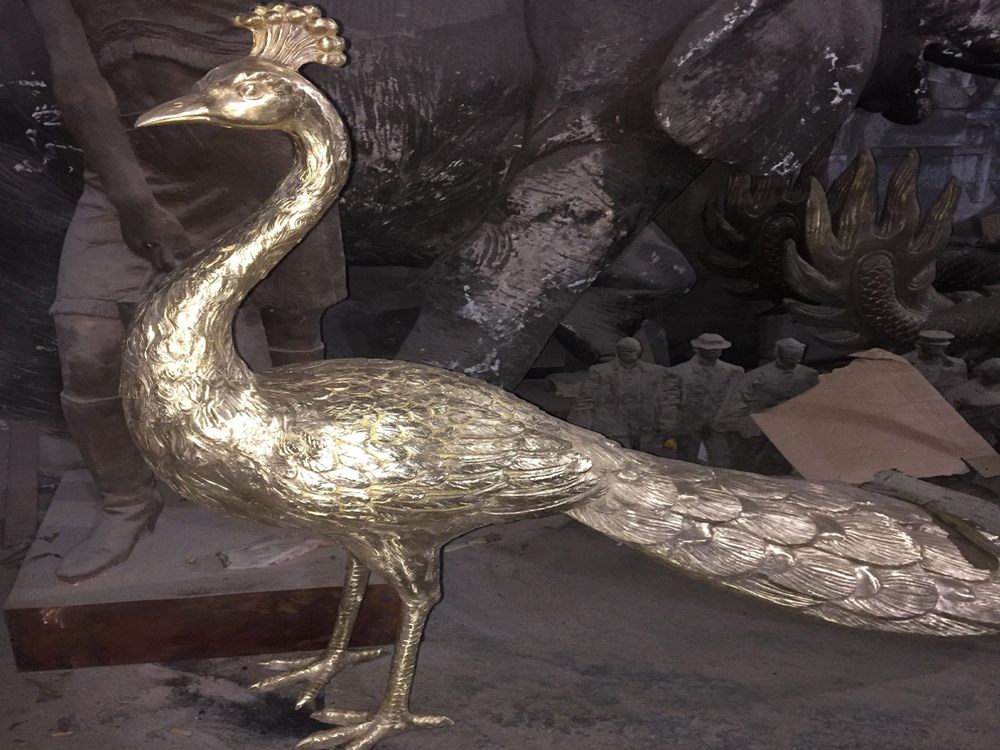
Welding or joining bronze pieces presents unique challenges due to the metal's composition and properties. One of the most common issues is oxidation, as bronze readily forms a surface oxide layer that can hinder proper fusion. This requires thorough cleaning and sometimes the use of flux to ensure a strong bond.
Another challenge is bronze's heat sensitivity. Excessive heat can warp or weaken the material, making precise temperature control essential. Techniques like TIG welding or brazing are often preferred to minimize heat distortion.
Selecting the right filler metal is also critical. Mismatched filler alloys can lead to weak joints or corrosion over time. Silicon bronze filler rods are a popular choice for their compatibility and strength.
Additionally, bronze's thermal conductivity can cause uneven heating, leading to inconsistent welds. Skilled welders often preheat the workpiece to distribute heat more evenly.
Lastly, post-weld cooling must be managed carefully to prevent cracking. Slow, controlled cooling is recommended to maintain the integrity of the joint. By understanding and addressing these challenges, craftsmen can achieve durable and aesthetically pleasing bronze welds.