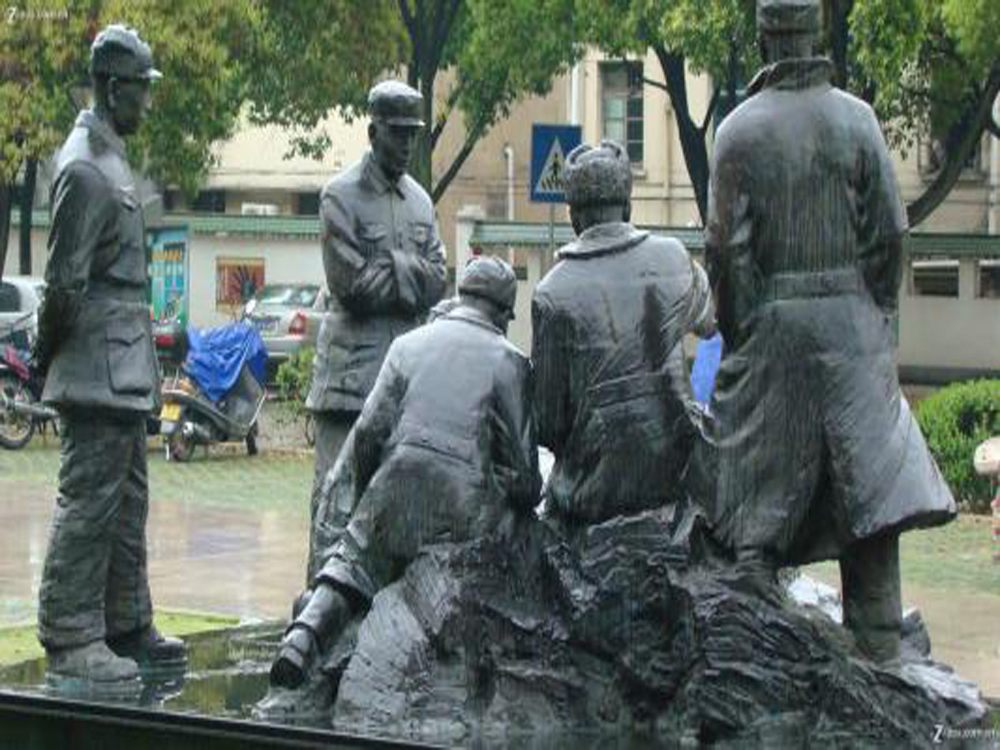
The creation of bronze sculptures involves intricate metal casting techniques, with lost-wax casting and sand casting being two of the most prominent methods. While both processes yield stunning results, they differ significantly in precision, complexity, and final output.
Lost-wax casting, also known as investment casting, is renowned for its ability to capture fine details. The process begins with a wax model, which is coated in a ceramic shell. Once the shell hardens, the wax is melted away, leaving a hollow mold. Molten bronze is then poured into this mold, solidifying into a highly detailed sculpture. This method is favored for its accuracy and ability to reproduce intricate designs, making it ideal for artistic and small-scale productions.
Sand casting, on the other hand, uses compacted sand to create a mold. A pattern is pressed into the sand, which is then removed to form a cavity for the molten bronze. While sand casting is faster and more cost-effective for larger pieces, it lacks the precision of lost-wax casting. The texture of the sand often leaves a rougher surface, requiring additional finishing work.
Key differences include:
1. Detail and Precision: Lost-wax casting excels in capturing fine details, while sand casting is better suited for simpler, larger forms.
2. Cost and Time: Sand casting is generally quicker and cheaper, especially for mass production, whereas lost-wax casting demands more time and resources.
3. Surface Finish: Lost-wax produces smoother surfaces, while sand casting often requires post-casting polishing.
Ultimately, the choice between these methods depends on the artist’s goals—whether prioritizing detail or efficiency. Both techniques contribute uniquely to the timeless art of bronze sculpture.