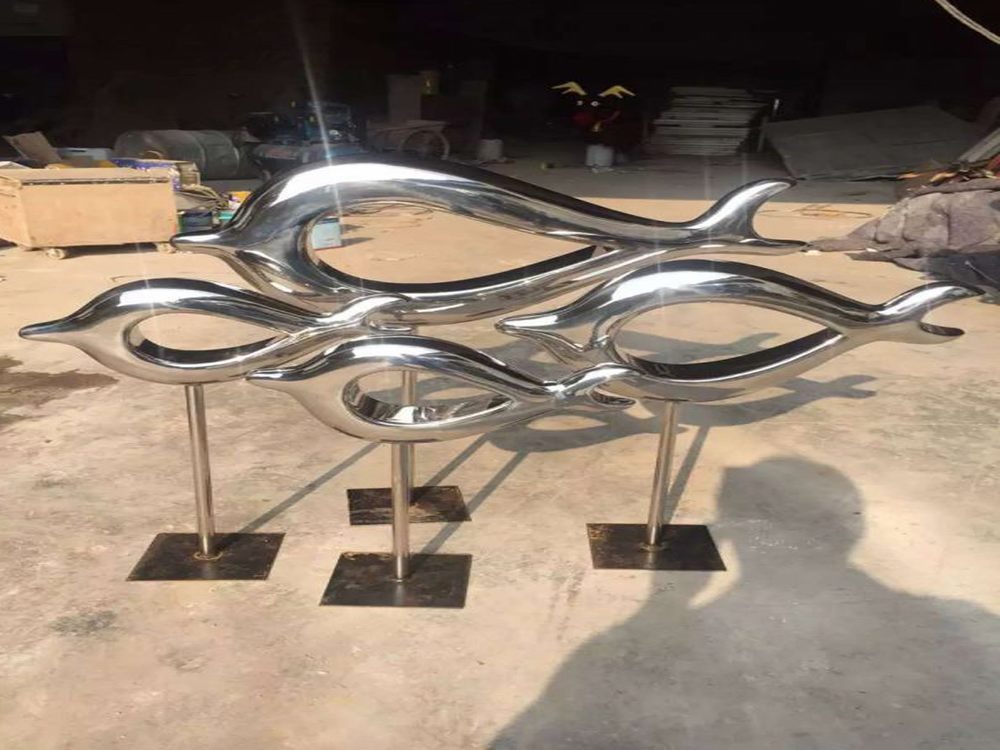
Commissioning a custom bronze sculpture is an exciting journey that transforms artistic vision into a timeless masterpiece. The process involves several critical steps to ensure the final piece meets your expectations.
1. Conceptualization and Design:
The process begins with a detailed discussion between the client and the sculptor. Ideas, themes, and inspirations are shared, followed by sketches or digital renderings to visualize the design.
2. Creating a Clay Model:
Once the design is approved, the sculptor crafts a clay model. This stage allows for adjustments and refinements to capture the desired details and proportions.
3. Mold Making:
The clay model is used to create a flexible mold, often made of silicone or rubber. This mold will serve as the foundation for the wax version of the sculpture.
4. Wax Casting and Refinement:
Molten wax is poured into the mold to create a replica of the original model. The wax is then meticulously refined to perfect every detail before the bronze casting begins.
5. Bronze Casting:
The wax model is coated in a ceramic shell and heated, allowing the wax to melt away. Molten bronze is poured into the shell, creating the final sculpture.
6. Patina and Finishing:
The bronze sculpture is treated with chemicals to achieve the desired patina, enhancing its texture and color. A protective coating is applied to preserve the finish.
7. Installation and Delivery:
The completed sculpture is mounted on a base or installed at the designated location, ready to be admired for generations.
By following these steps, a custom bronze sculpture becomes a unique and enduring work of art, reflecting the client’s vision and the sculptor’s skill.