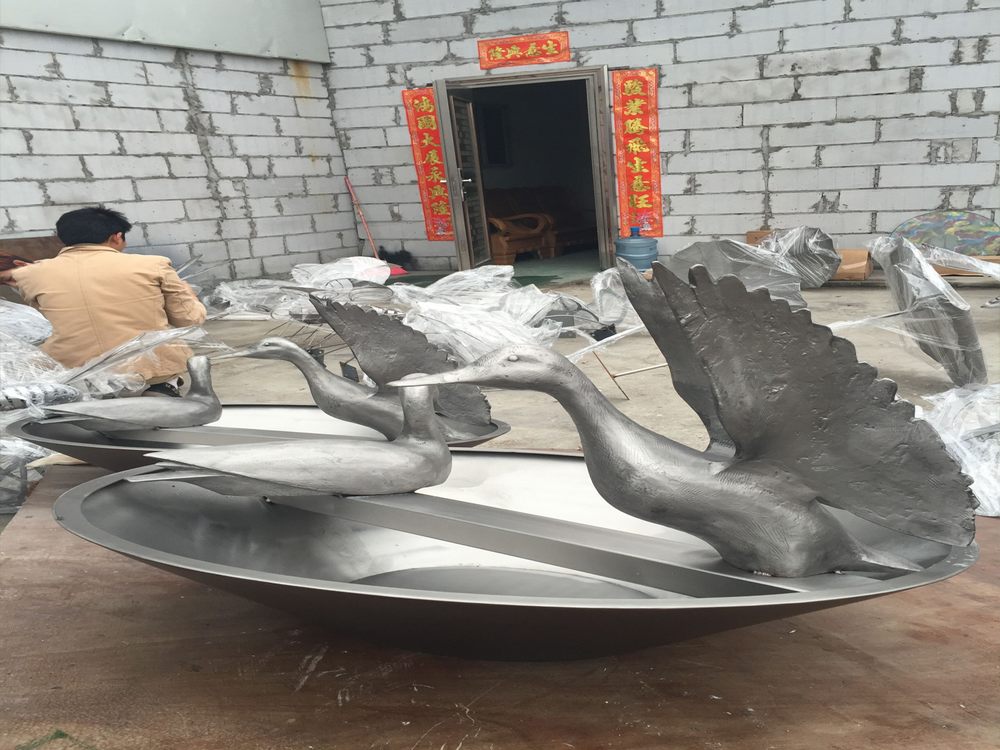
Bronze sculptures have been cherished for centuries, but not all bronze artworks are created the same way. The two primary methods—cold-cast and hot-cast bronze—produce strikingly different results in terms of texture, durability, and artistic expression.
1. Production Process
Hot-cast bronze sculptures are made using the traditional lost-wax method, where molten bronze is poured into a ceramic mold at extremely high temperatures. This technique dates back thousands of years and requires skilled craftsmanship. In contrast, cold-cast bronze involves mixing bronze powder with resin and pouring it into a mold at room temperature, resulting in a faster and more cost-effective process.
2. Material Composition & Weight
Hot-cast sculptures are solid bronze, giving them substantial weight and an authentic metallic feel. Cold-cast pieces, however, are lighter due to the resin base, though the surface contains real bronze particles for a metallic appearance.
3. Surface Detail & Texture
Hot-casting captures finer details and produces a richer, deeper patina over time. Cold-cast sculptures may lack the same depth but can still achieve a convincing bronze-like finish with proper polishing and coating.
4. Durability & Longevity
Hot-cast bronze is highly durable and resistant to weathering, making it ideal for outdoor installations. Cold-cast pieces are more susceptible to wear and are better suited for indoor display.
5. Cost & Accessibility
Due to the intensive labor and materials required, hot-cast bronze sculptures are significantly more expensive. Cold-cast bronze offers an affordable alternative for collectors who appreciate the bronze aesthetic without the premium price.
Whether you prefer the timeless authenticity of hot-cast bronze or the modern convenience of cold-cast, understanding these differences helps in selecting the perfect sculpture for your collection.