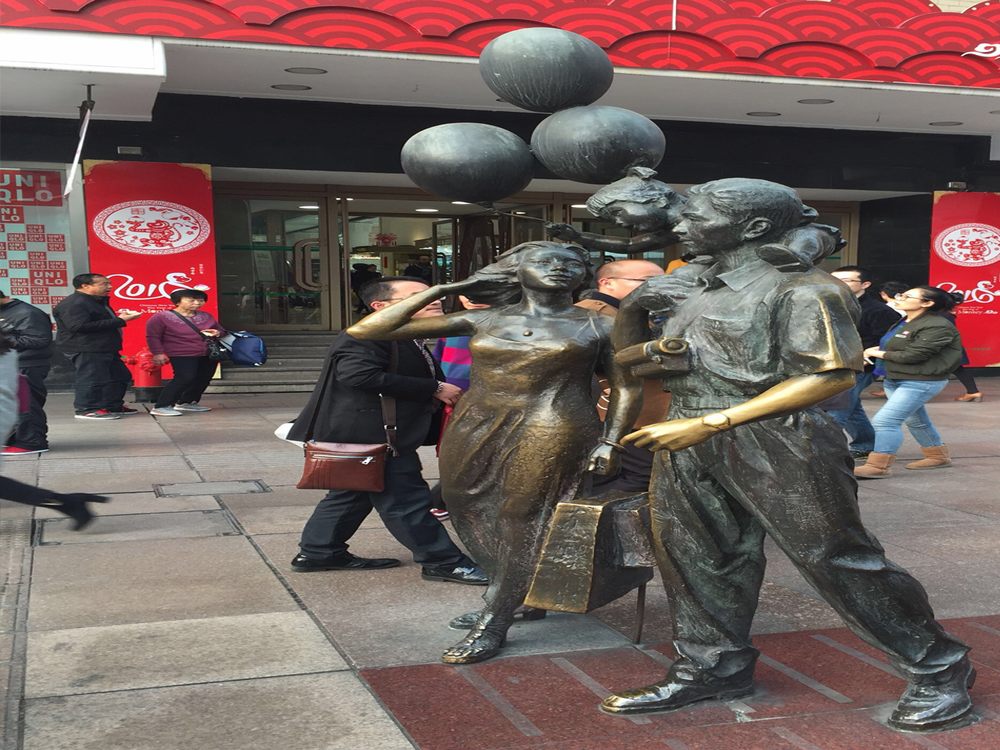
Creating hollow bronze sculptures is a revered yet demanding art form that combines technical precision with artistic vision. Here are the most common challenges artists face and practical solutions to address them:
1. Complex Casting Process
Hollow bronze sculptures require intricate lost-wax casting, where even minor flaws in the mold can ruin the final piece. Artists must master gating systems to ensure even metal flow while preventing air pockets.
2. Structural Integrity
Thin bronze walls risk collapsing during casting or cracking over time. Reinforcing internal armatures and calculating optimal thickness (typically 3-8mm) is crucial for durability without compromising elegance.
3. Thermal Management
Bronze shrinks 1.5% during cooling, potentially warping delicate sections. Experienced founders control cooling rates by strategically heating different zones of the mold.
4. Weight Distribution
Large hollow sculptures need careful balance planning. Many artists create small-scale maquettes first to test center of gravity, especially for dynamic poses.
5. Patina Consistency
Achieving uniform chemical patinas on hollow sections demands specialized techniques like controlled fuming or compartmentalized acid application to account for varying metal thicknesses.
Pro tip: Contemporary sculptors increasingly combine traditional methods with 3D-printed ceramic molds and computational fluid dynamics simulations to predict casting behavior. The key lies in respecting bronze's material properties while pushing creative boundaries – a dance between ancient craftsmanship and modern innovation that continues to elevate this timeless art form.