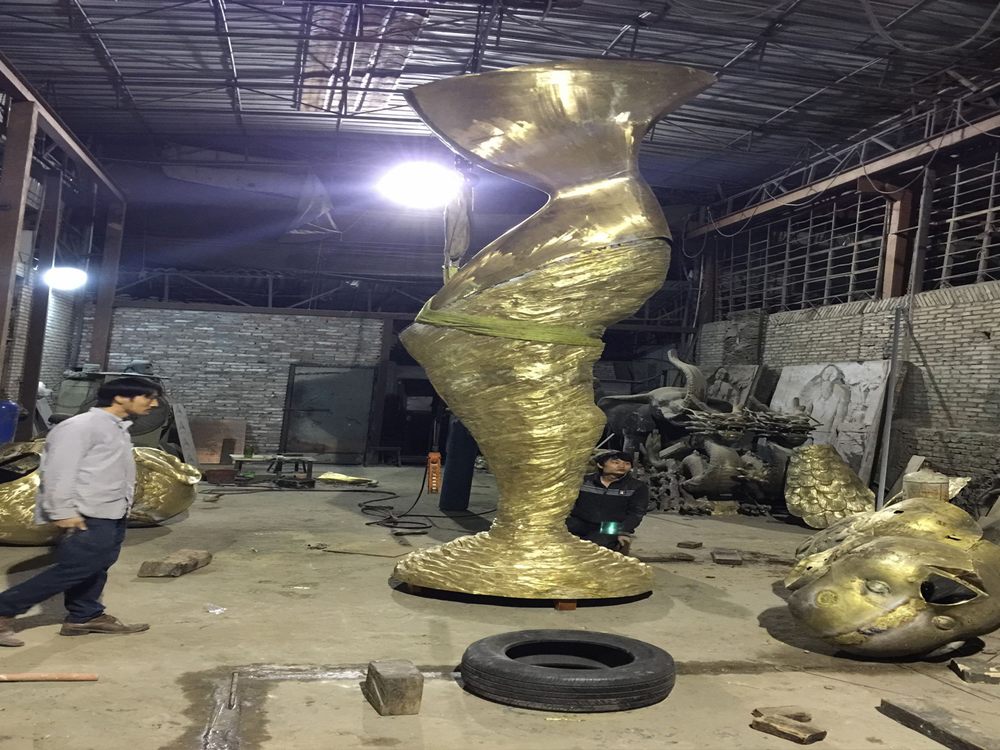
Creating bronze sculptures with movable parts is a fascinating yet complex endeavor that blends artistry with engineering. One of the most common challenges is achieving precise alignment during the casting process. Bronze shrinks as it cools, which can distort joints and hinges, making movement difficult or impossible. Artists must account for this shrinkage in their designs, often requiring multiple iterations.
Another significant hurdle is ensuring durability. Movable parts experience friction and wear over time, which can degrade the sculpture's functionality. Selecting the right bronze alloy and incorporating durable pivot points, such as stainless steel pins, is crucial for longevity.
Balancing aesthetics and mechanics is also tricky. The artist must hide or integrate mechanical components seamlessly without compromising the sculpture's visual appeal. This often demands innovative solutions, like concealed hinges or internal counterweights.
Lastly, environmental factors pose challenges. Outdoor sculptures with movable parts must withstand weather conditions, requiring protective coatings and regular maintenance to prevent corrosion or seizing.
Despite these obstacles, mastering the art of kinetic bronze sculptures results in captivating works that merge motion and beauty.