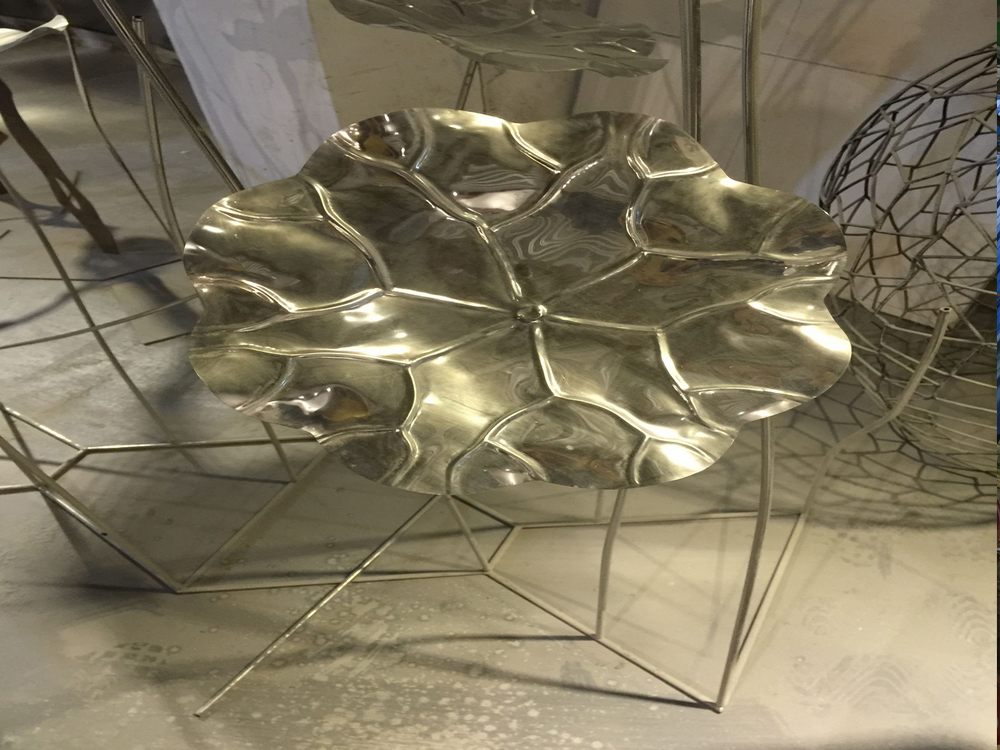
Bronze casting has been a revered artistic and functional metalworking technique for millennia, with solid and hollow methods representing two distinct approaches. The most significant differences between these techniques lie in their processes, material usage, and final outcomes.
Solid bronze casting involves pouring molten bronze into a mold until completely filled, creating a dense, heavy object. This method excels in producing small, durable items like jewelry or hardware where weight isn't a concern. The process is relatively straightforward but consumes more material, making it costlier for large pieces. Solid castings offer superior structural integrity and thermal properties, ideal for functional components requiring heat resistance.
Hollow bronze casting, typically achieved through the lost-wax method, creates lighter sculptures with interior cavities. Artists favor this technique for monumental works where weight reduction is crucial for installation and transportation. The process involves creating a wax model, coating it with ceramic, then melting the wax to leave a hollow mold. While more complex, it uses less material and allows for intricate detailing. Hollow casting enables larger artworks at lower costs but may require internal supports for structural stability.
Material efficiency differs dramatically - hollow casting uses about 1/3 the bronze of solid casting for similar-sized pieces. Finishing processes also vary; solid castings often require less surface work, while hollow pieces may need welding of separately cast sections. The choice between techniques ultimately depends on artistic intent, budget, and practical considerations like installation requirements. Contemporary artists frequently combine both methods within single works to balance structural needs with creative vision.