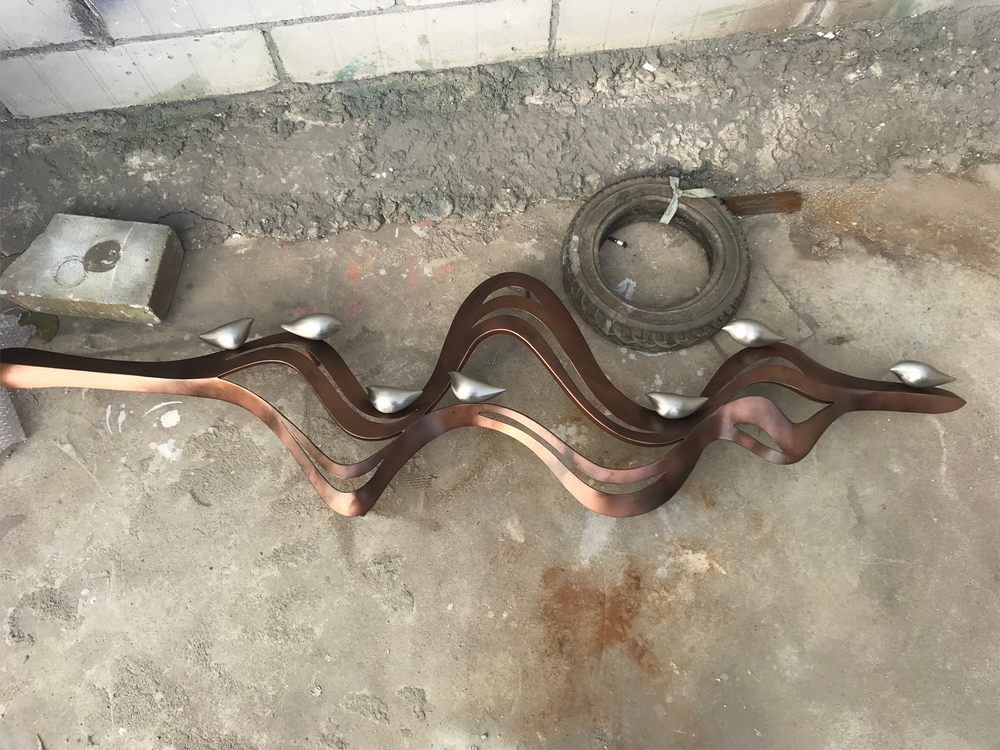
The creation of bronze models can be achieved through two distinct methods: hand-carving and machine-milling. While both produce stunning results, their differences lie in craftsmanship, precision, and artistic value.
Hand-carved bronze models are the product of skilled artisans who meticulously shape each detail by hand. This traditional approach allows for unique imperfections that add character and authenticity to the piece. The process is time-consuming but results in one-of-a-kind artworks with organic textures and subtle variations. Art collectors often prize hand-carved pieces for their human touch and historical significance.
Machine-milled bronze models, by contrast, are created using computer-controlled equipment that follows precise digital designs. This modern technique delivers flawless consistency and perfect symmetry, making it ideal for industrial applications or reproduction work. The milling process can achieve intricate details that might challenge even the most skilled human hand, but some argue it lacks the soul of handmade pieces.
Durability differs as well. Hand-carved bronze often has thicker walls and more substantial material distribution, as the artist can adjust for structural integrity. Machine-milled pieces may have thinner, more uniform walls that maximize material efficiency but could compromise longevity in some applications.
Cost and time factors separate these methods significantly. Hand-carving requires extensive labor and expertise, making it more expensive and time-intensive. Machine-milling offers faster production and lower costs for identical reproductions, though initial setup expenses can be high.
Ultimately, the choice between hand-carved and machine-milled bronze depends on your priorities: unique artistry versus perfect precision, traditional craftsmanship versus modern efficiency. Both methods have their place in bronze work, serving different needs in art, industry, and collectibles.