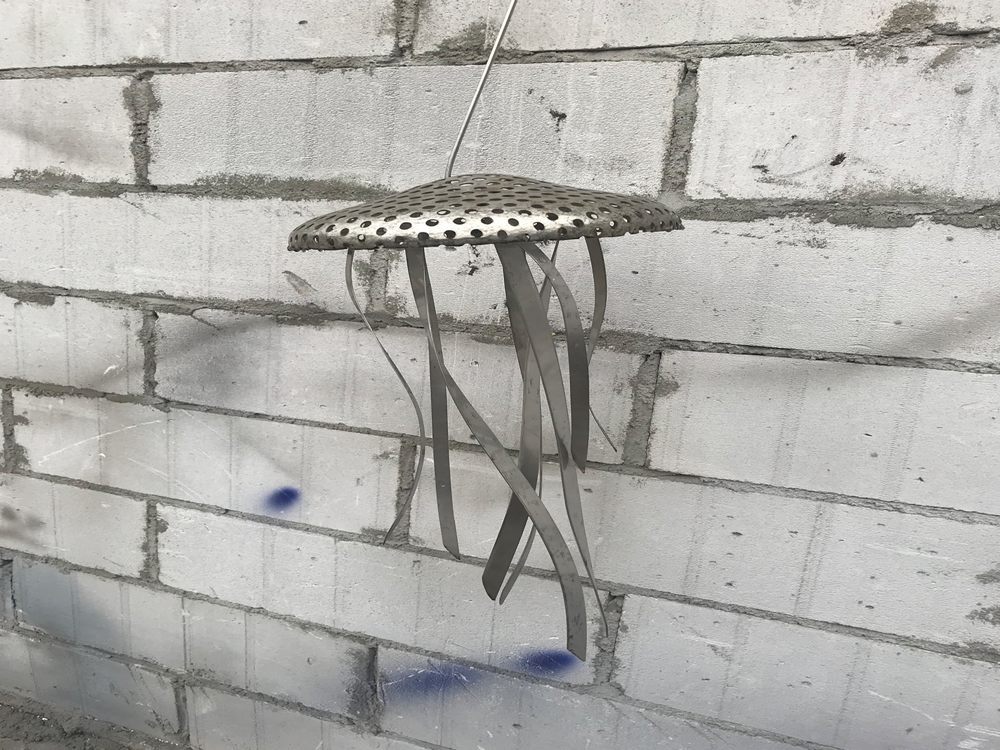
Creating metal sculptures that achieve both visual complexity and structural soundness presents a unique set of challenges for artists and metalworkers. The first major hurdle lies in material selection - metals behave differently under stress, and choosing the wrong alloy can lead to catastrophic failures in ambitious designs.
Weight distribution becomes particularly problematic when working with intricate, asymmetrical forms. Artists must calculate load-bearing points while maintaining aesthetic flow, often requiring hidden supports that don't compromise the visual concept. Welding techniques present another layer of difficulty, as complex joints in thin metal sections can weaken the overall structure if not executed with precision.
Thermal expansion introduces unexpected variables, especially for large outdoor installations that experience temperature fluctuations. What appears stable in the studio may warp or crack when exposed to sunlight or freezing conditions. Many sculptors combat this through strategic segmentation, creating the illusion of continuous form while actually building in expansion joints.
The finishing process also presents dilemmas - intricate surface treatments like acid etching or patinas can actually weaken the metal if not properly sealed. This forces artists to make difficult choices between durability and desired visual effects.
Successful metal sculptors often collaborate with engineers, using computer modeling to test designs before fabrication. Modern techniques like 3D metal printing are opening new possibilities, though traditional craftsmanship remains essential for achieving both artistic vision and structural reliability in these demanding works.