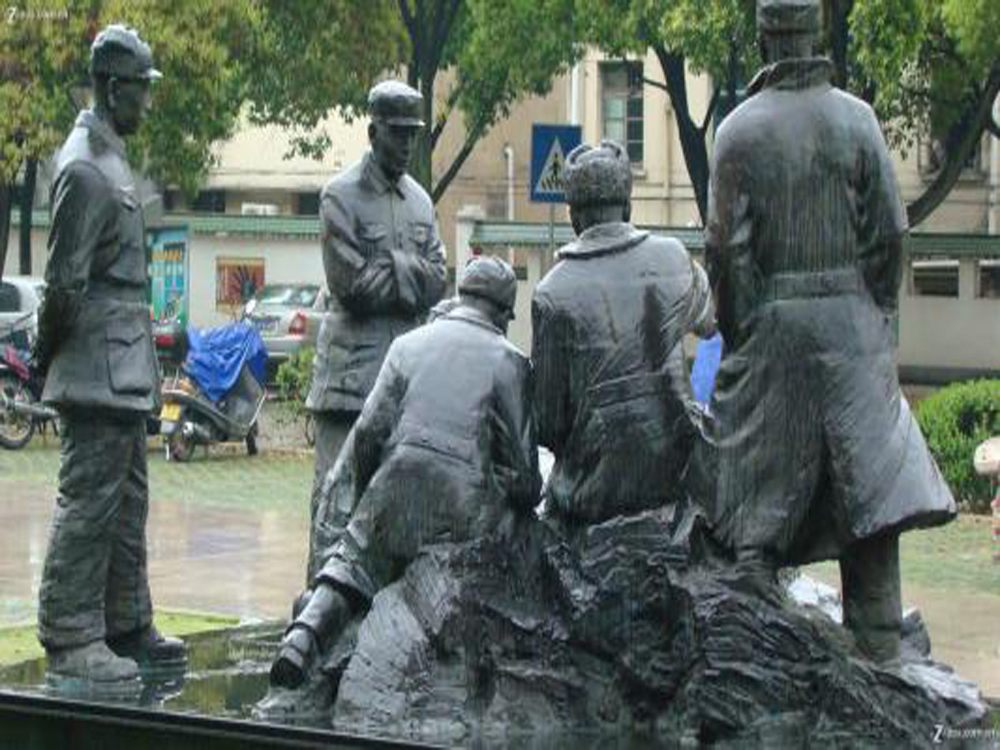
When it comes to achieving a flawless metal finish, two primary methods stand out: hand-polishing and electro-polishing. While both techniques enhance the appearance and durability of metal surfaces, they differ significantly in process, results, and applications.
Hand-polishing is a manual process where abrasives, buffing wheels, and polishing compounds are used to create a smooth, reflective surface. This method allows for greater control over the final finish, making it ideal for decorative pieces, architectural elements, and custom metalwork. However, it can be time-consuming and may leave minor imperfections visible under close inspection.
Electro-polishing, on the other hand, is an electrochemical process that removes a thin layer of metal from the surface. The metal part is submerged in an electrolyte solution and subjected to an electric current, resulting in a microscopically smooth, ultra-clean finish. This method is preferred for medical equipment, food processing machinery, and semiconductor components where hygiene and corrosion resistance are critical.
Key differences include:
1. Surface Quality: Electro-polishing produces a more uniform, contamination-free surface compared to hand-polishing.
2. Durability: Electro-polished finishes typically offer superior corrosion resistance due to the removal of surface impurities.
3. Precision: Hand-polishing allows for artistic customization, while electro-polishing ensures consistent industrial-grade results.
4. Cost: Hand-polishing is labor-intensive, whereas electro-polishing requires specialized equipment but can be more cost-effective for large batches.
Choosing between these methods depends on your project requirements. For aesthetic applications, hand-polishing offers unmatched craftsmanship. For functional or sanitary applications, electro-polishing delivers unmatched performance. Understanding these differences ensures you select the right finish for your metal components.