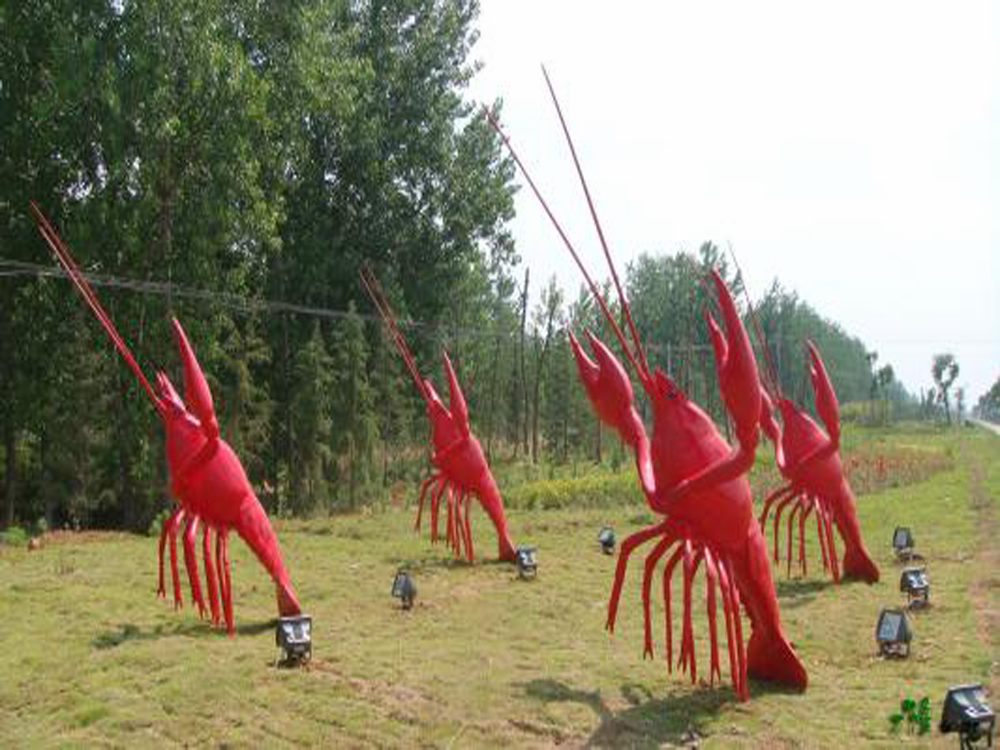
Creating large-scale bronze sculptures is a complex interplay of artistry and engineering. Artists employ meticulous techniques to ensure structural integrity, beginning with a robust internal framework. Typically, stainless steel or bronze armatures are used to support the weight and prevent deformation.
The lost-wax casting process, a cornerstone of bronze sculpture, involves creating a detailed wax model coated in ceramic shell. Once melted away, molten bronze fills the cavity, but artists must account for metal shrinkage and stress points. Strategic gating systems and venting channels are incorporated to ensure even cooling and prevent cracks.
For monumental works, segmented casting is often employed. The sculpture is divided into manageable sections, cast separately, and later welded together with precision. Reinforcement rods and internal bracing are added to withstand environmental stresses like wind and temperature fluctuations.
Modern artists also leverage digital tools, using 3D modeling to simulate stress points and optimize weight distribution. Finally, periodic maintenance, including patina treatments and structural inspections, ensures longevity. Through these methods, artists transform molten metal into enduring masterpieces.