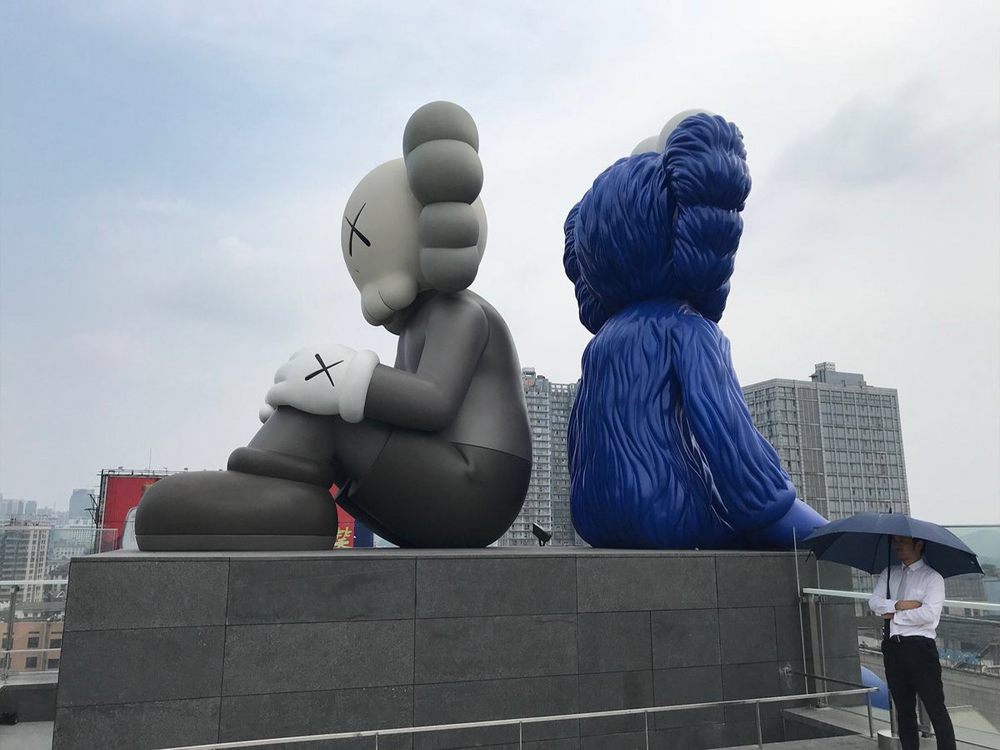
Foundries play a crucial role in metalworking, and managing excess bronze during casting is essential for both economic and environmental sustainability. Here’s how they tackle this challenge:
1. Scrap Collection Systems – Modern foundries use automated scrap collection systems to gather leftover bronze from molds, spills, and trimmings. This material is immediately sorted and prepared for reuse.
2. Remelting and Purification – Excess bronze is remelted in specialized furnaces. Impurities are removed through fluxing or filtration, ensuring the recycled metal meets quality standards for new castings.
3. Closed-Loop Recycling – Many foundries adopt closed-loop systems where nearly all excess bronze is reintroduced into production cycles, minimizing raw material waste.
4. Alloy Adjustment – Since recycled bronze may vary in composition, foundries carefully adjust alloy ratios by adding pure metals or other scrap blends to maintain consistency.
5. Waste-to-Product Partnerships – Some foundries collaborate with external recyclers to repurpose lower-grade bronze scraps into non-critical products like decorative items or industrial components.
By implementing these strategies, foundries reduce costs, lower environmental impact, and contribute to a circular economy in metal manufacturing. Advanced technologies like induction melting and real-time alloy analysis further enhance recycling efficiency.
Sustainable bronze recycling not only conserves resources but also aligns with global efforts to minimize industrial waste, making it a win-win for manufacturers and the planet.