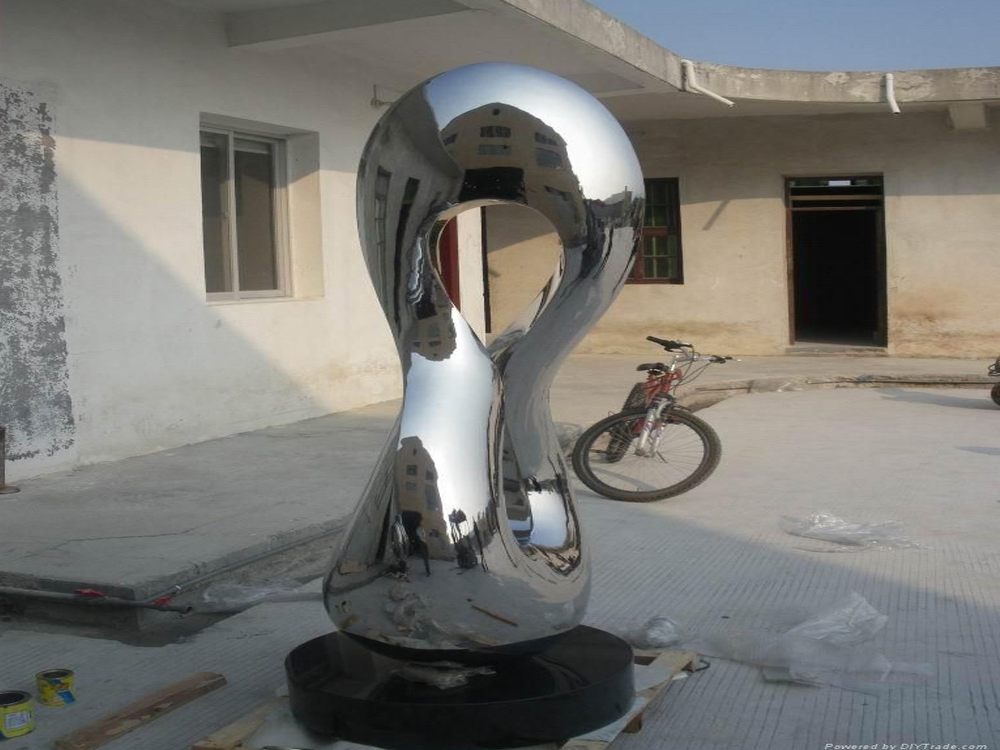
Casting bronze sculptures with undercuts or complex geometries presents unique challenges that test the limits of traditional foundry techniques. One major hurdle is the creation of a reusable mold—undercuts make it difficult to extract the original model without damaging the mold. The lost-wax process, while versatile, struggles with deep recesses where wax may become trapped during burnout, leading to incomplete metal fills.
Complex geometries also increase the risk of uneven cooling, causing stress fractures or warping in the final piece. Thin protruding elements are particularly vulnerable to breaking during demolding or finishing. Additionally, intricate designs require meticulous chasing and patination work to preserve details, significantly extending production time.
Modern solutions include segmented molds or 3D-printed ceramic shells, but these often come with higher costs and technical barriers. Ultimately, artists must balance creative ambition with the physical realities of metal casting to achieve successful results.