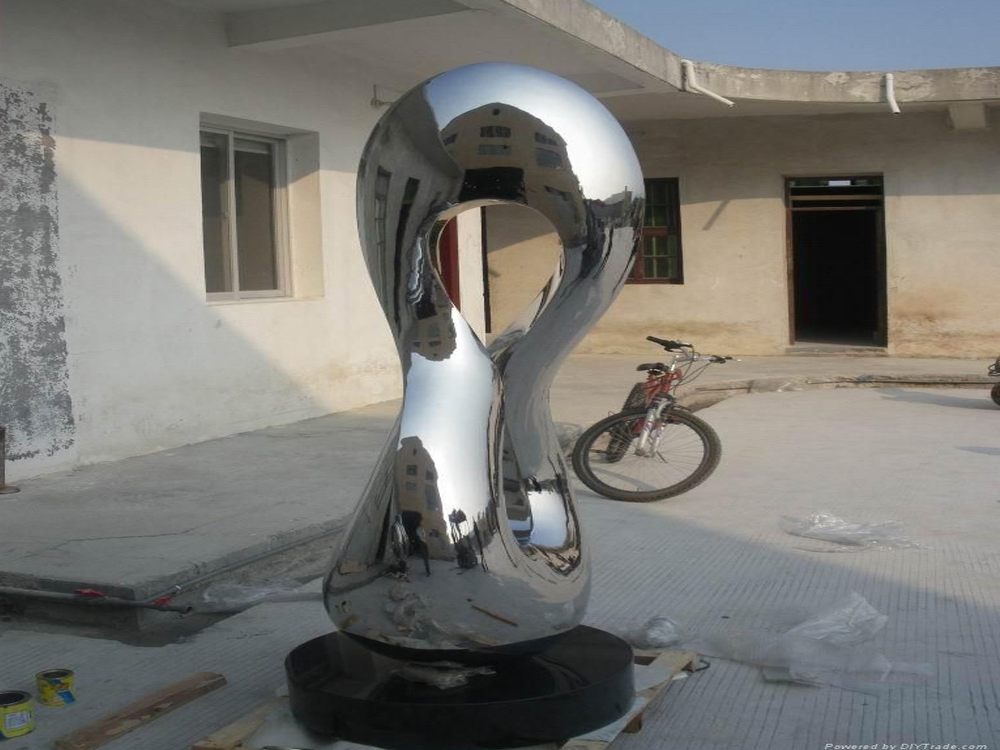
Casting thin-walled bronze sculptures is a delicate art form that demands precision and expertise. One of the most frequent challenges is maintaining mold integrity. Thin walls require exceptionally stable molds, as even minor shifts can lead to deformities or cracks. Artists often use ceramic shell molds for their strength and fine detail retention.
Another critical issue is controlling the cooling rate. Bronze contracts as it cools, and uneven cooling can cause warping or stress fractures. To mitigate this, foundries may preheat molds or adjust pouring temperatures. Additionally, achieving uniform wall thickness is tricky but vital—variations can create weak spots or aesthetic flaws.
Gating systems also pose difficulties. Proper venting and sprue placement are essential to ensure molten bronze flows evenly without trapping air. Lastly, surface finishing requires extra care, as thin walls are more prone to imperfections during polishing and patination. Mastering these challenges separates amateur attempts from professional-grade bronze artistry.