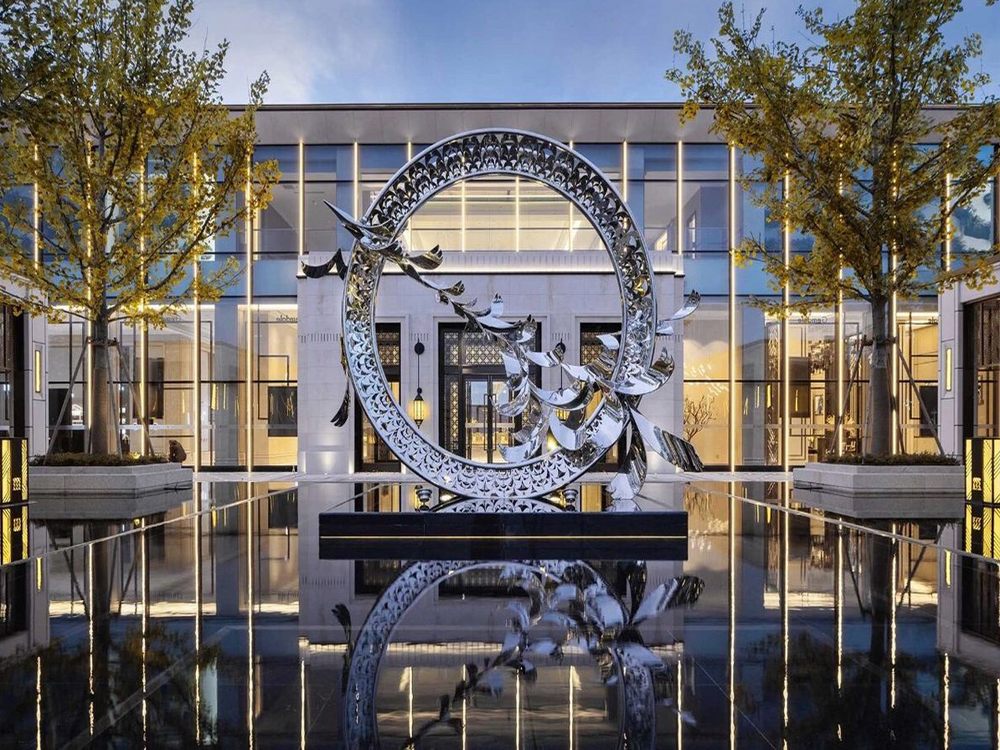
Thermal stress cracks in bronze can compromise structural integrity and aesthetics, but they can be prevented with proper techniques. One of the most effective methods is controlled cooling after casting. Rapid cooling creates internal stresses, so gradual cooling in a furnace or insulated environment reduces crack risks.
Choosing the right bronze alloy is also crucial. Alloys with higher tin or aluminum content, such as aluminum bronze, often exhibit better resistance to thermal stress. Additionally, preheating molds before casting minimizes temperature differentials, reducing the likelihood of cracks.
Heat treatment processes like annealing help relieve residual stresses. By heating bronze to a specific temperature and slowly cooling it, internal stresses are redistributed evenly. Proper design considerations, such as avoiding sharp corners and thick-thin transitions, further prevent stress concentration.
Lastly, monitoring environmental conditions during casting and post-processing ensures consistent thermal management. Implementing these methods significantly reduces thermal stress cracks, enhancing bronze durability and performance.