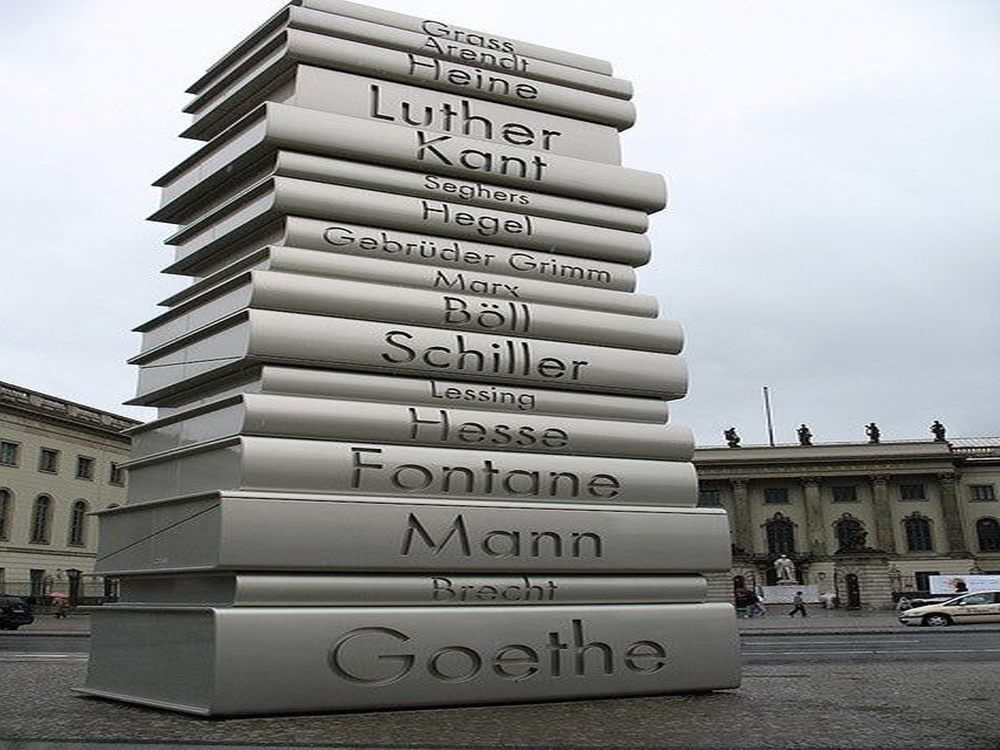
Creating bronze sculptures with intricate details is a complex art form that demands precision and expertise. One of the most common challenges is metal shrinkage, as bronze contracts during cooling, potentially distorting fine features. Artists must account for this by carefully scaling their models.
Another hurdle is mold-making imperfections. The lost wax casting process, while highly detailed, can introduce tiny flaws if the mold isn’t perfectly prepared. Air bubbles or uneven wax layers may compromise the final piece.
Heat management is also critical. Overheating can weaken delicate structures, while insufficient heat may cause incomplete pours. Additionally, tooling and finishing require immense skill to preserve fine details without over-polishing or damaging the surface.
Lastly, material costs and time pose practical challenges. High-quality bronze and repeated casting trials increase expenses, while achieving flawless results often demands patience and multiple iterations. Mastering these challenges separates exceptional sculptors from the rest.