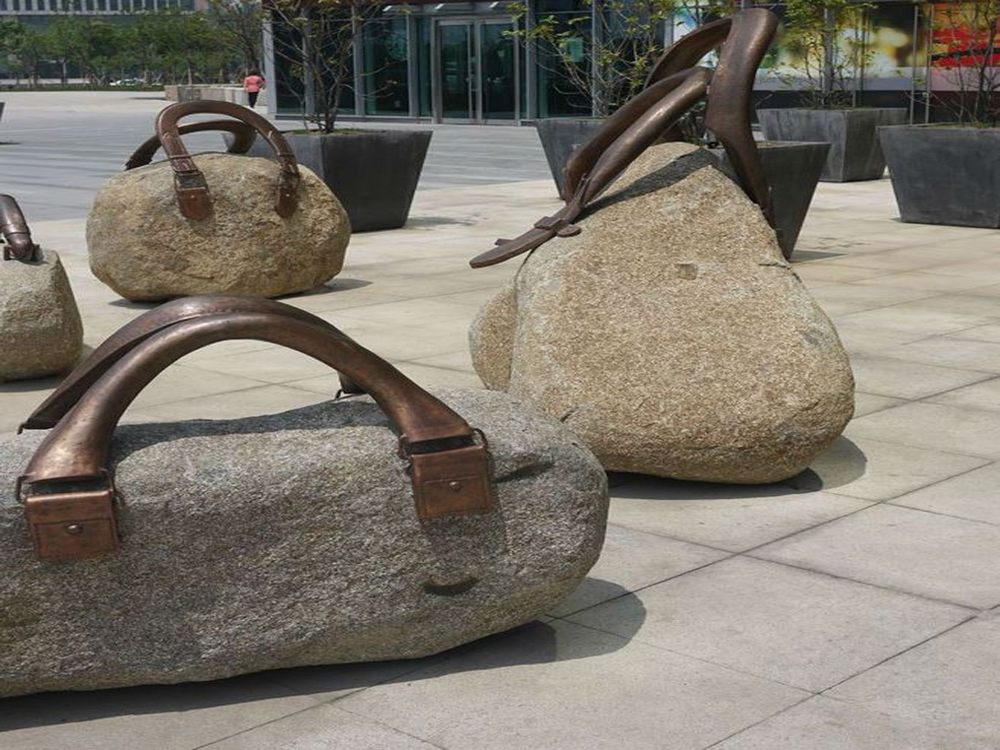
Bronze casting has been a revered art form for millennia, but modern artists and foundries are pushing boundaries with experimental techniques. Traditional bronze casting, rooted in ancient practices like lost-wax (cire perdue) and sand casting, emphasizes meticulous craftsmanship and time-honored metallurgical knowledge. These methods typically involve creating a wax model, encasing it in refractory material, and pouring molten bronze into the resulting mold cavity.
Experimental approaches, by contrast, incorporate innovative materials and technologies. Some artists use 3D-printed molds or digital modeling to create complex geometries impossible with traditional methods. Others experiment with alternative alloys, patinas, or even incorporate mixed media during the casting process. Where traditional casting might take weeks to complete a single piece, some experimental methods can accelerate production while allowing for greater artistic risk-taking.
The finishes also differ markedly - traditional bronzes often feature classical patinas achieved through chemical treatments, while experimental pieces may showcase raw, textured surfaces or unconventional color treatments. Both approaches continue to evolve, with traditional methods preserving cultural heritage while experimental techniques expand bronze's possibilities in contemporary art.