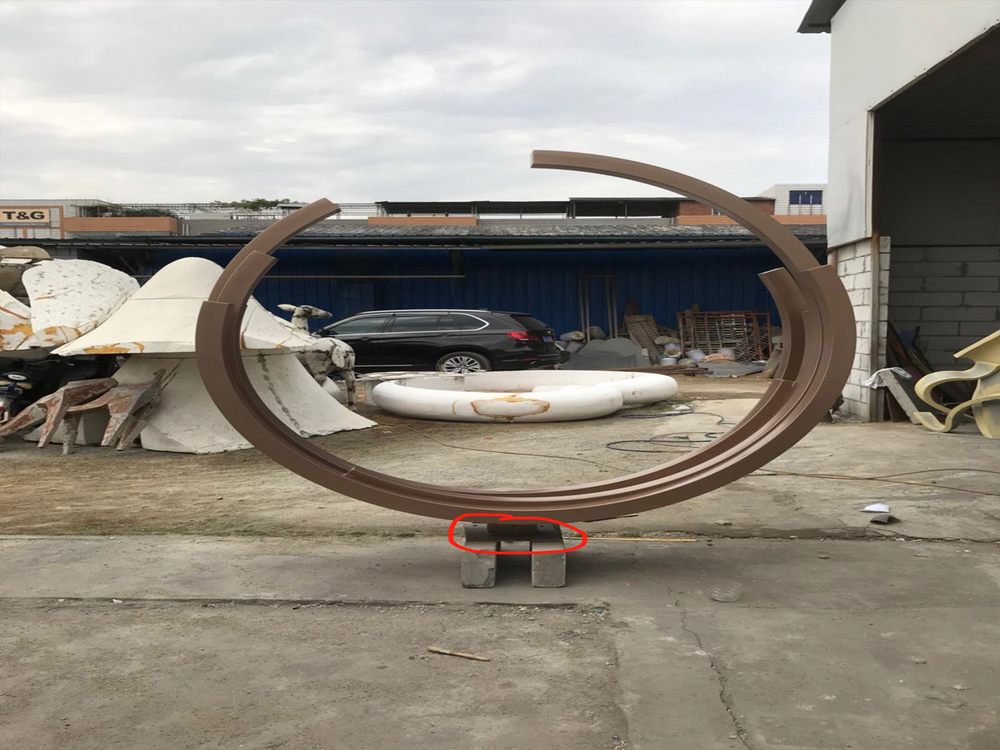
Creating bronze sculptures with articulated joints is a complex and demanding process that combines artistry with engineering. One of the most common challenges is achieving precise joint articulation while maintaining structural integrity. Bronze, though durable, can be brittle, making it difficult to craft movable parts without risking breakage.
Another issue is the metal casting process itself. Ensuring that joints align perfectly after casting requires meticulous planning and precise mold-making. Any imperfections can lead to stiff or non-functional joints, compromising the sculpture's intended movement.
Additionally, thermal expansion and contraction during cooling can warp joints, requiring post-casting adjustments. Artists must also consider long-term durability, as repeated movement can wear down joint surfaces over time.
Balancing aesthetics with functionality is another hurdle. Sculptors must design joints that are both visually seamless and mechanically sound, often requiring multiple prototypes. Despite these challenges, mastering articulated bronze sculptures results in stunning, dynamic artworks that captivate viewers.