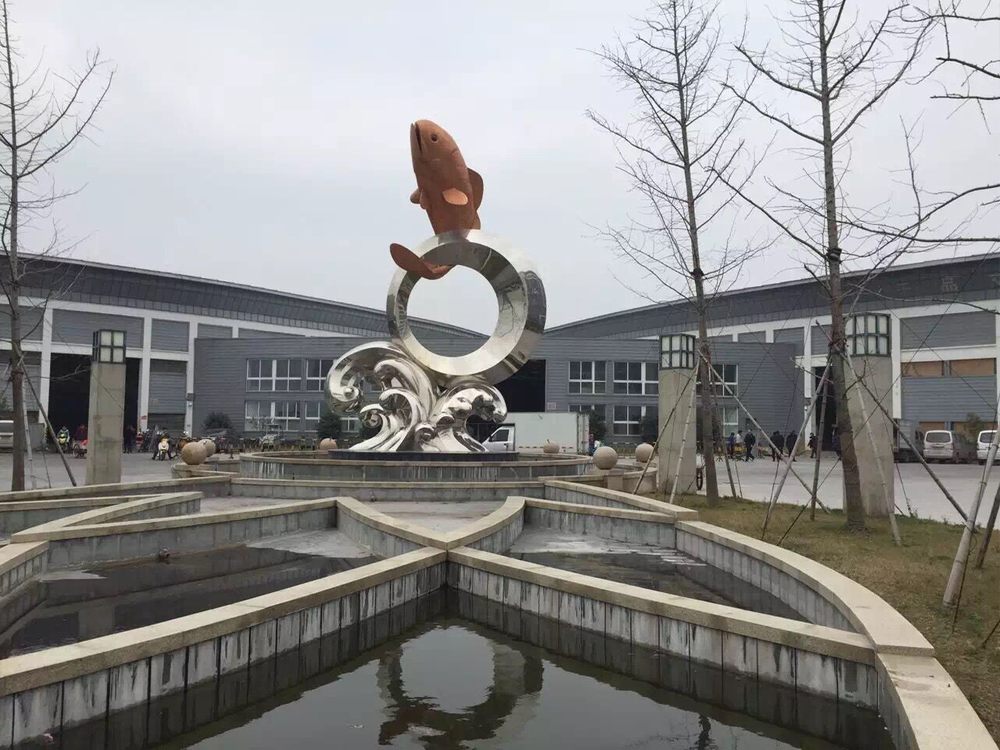
Creating bronze sculptures with modular components presents a unique set of challenges that test both artistic vision and technical skill. One major hurdle is achieving precise casting tolerances—even minor variations in individual modules can lead to visible gaps or misalignment during assembly. Artists must also consider the thermal expansion of bronze, as temperature fluctuations during the casting process may cause components to fit differently than intended.
Another significant challenge lies in the welding and joining process. Unlike single-cast sculptures, modular pieces require flawless seams that maintain structural integrity while remaining visually undetectable. This demands exceptional metalworking expertise and often necessitates specialized techniques like TIG welding or custom patination to conceal joins.
Weight distribution becomes increasingly complex with modular designs. Each component must be engineered to support not only its own mass but also the cumulative load of attached elements. This frequently requires internal armatures or support systems that don't compromise the sculpture's aesthetic flow.
Finally, maintaining consistent patina across separately cast modules proves difficult due to variations in cooling rates and metal composition. Artists often spend considerable time color-matching sections to create a cohesive final appearance. Despite these challenges, modular bronze sculptures offer unparalleled creative possibilities, allowing for larger scales, intricate details, and innovative forms that would be impossible with traditional single-pour methods.