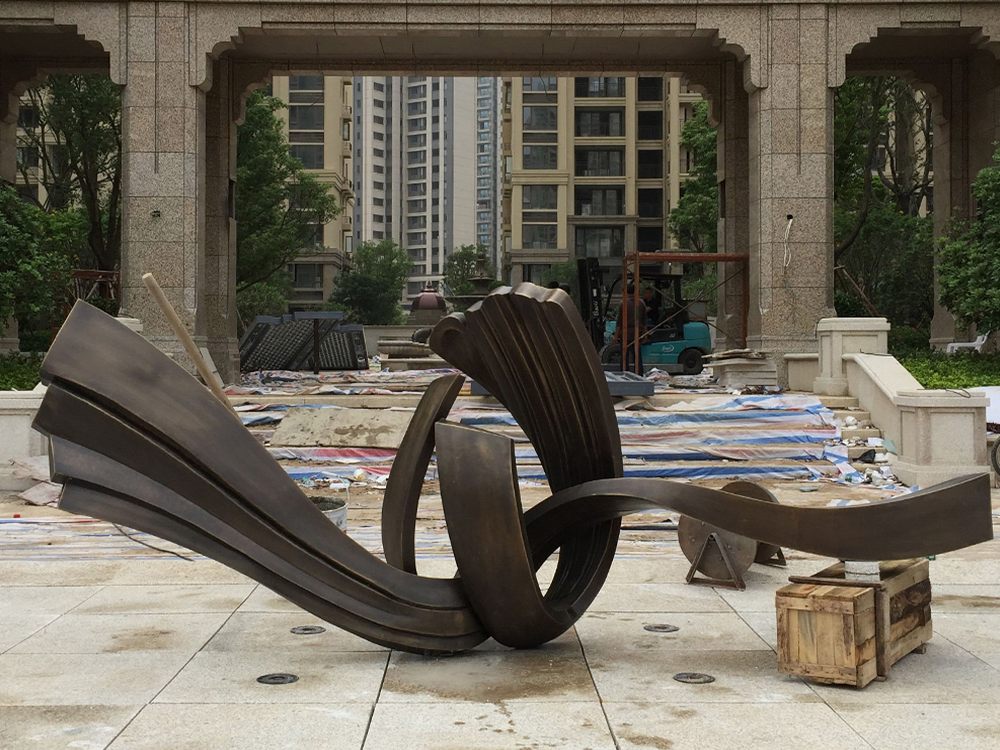
Intergranular corrosion in bronze alloys is a significant concern in industrial applications, as it weakens the material along grain boundaries, leading to premature failure. To combat this issue, several proven methods can be employed.
1. Alloy Composition Control: Adjusting the alloy's composition to minimize harmful impurities like phosphorus and sulfur can reduce susceptibility to intergranular corrosion. Adding elements like nickel or aluminum improves resistance by stabilizing the grain structure.
2. Heat Treatment: Solution annealing followed by rapid quenching helps redistribute alloying elements evenly, preventing harmful precipitates at grain boundaries. Stress-relief annealing also reduces residual stresses that accelerate corrosion.
3. Protective Coatings: Applying coatings such as lacquers, paints, or electroplated layers (e.g., nickel or tin) creates a barrier against corrosive environments. Regular maintenance of these coatings is essential for long-term protection.
4. Cathodic Protection: In marine or highly corrosive settings, sacrificial anodes or impressed current systems can shield bronze components from electrochemical degradation.
5. Environmental Control: Limiting exposure to chlorides, acids, and high-humidity conditions significantly slows intergranular corrosion. Proper storage and handling practices are critical.
By combining these methods, engineers can extend the lifespan of bronze alloys while maintaining their structural integrity in demanding applications.