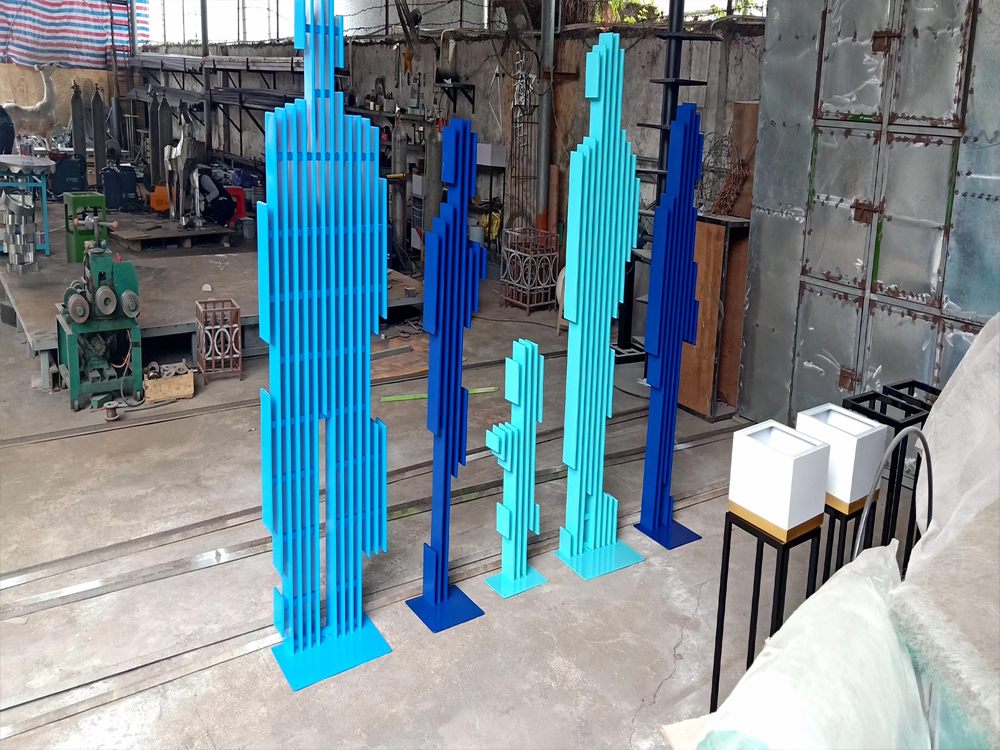
The wood carving industry, long rooted in manual craftsmanship, is undergoing a seismic shift due to advancements in 3D printing and laser carving technologies. These digital fabrication methods are disrupting traditional markets by offering unparalleled precision, speed, and customization.
3D printing enables artisans to create intricate wooden designs layer by layer, reducing material waste and production time. Complex geometries that once took weeks to carve by hand can now be produced in hours. Meanwhile, laser carving delivers razor-sharp detailing with computer-controlled accuracy, perfect for replicating patterns or creating bespoke pieces.
Traditional woodworkers face both challenges and opportunities. While mass-produced digital carvings threaten niche handcrafted markets, many artisans are adopting hybrid approaches—using these technologies for prototyping or combining them with manual finishing for unique pieces. The democratization of design tools also allows smaller workshops to compete with larger manufacturers.
Sustainability is another key advantage. Digital methods optimize material usage, and some 3D printers can even use recycled wood composites. However, debates continue about the loss of traditional skills and the "soul" of handmade pieces.
As these technologies become more accessible, the wood carving market is splitting into two segments: high-volume precision products made digitally, and premium handcrafted works that emphasize human artistry. The future likely holds a blended landscape where technology enhances rather than replaces traditional craftsmanship.