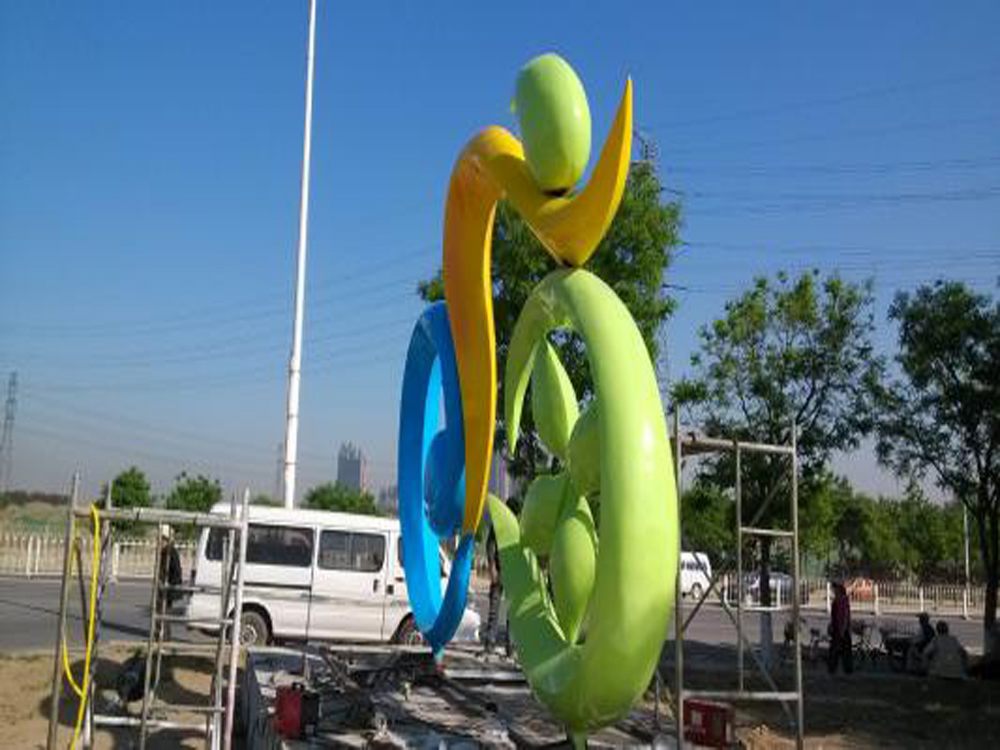
The wood carving industry, once dominated by hand tools and artisan craftsmanship, is undergoing a seismic shift with the advent of modern technologies like CNC machines and 3D carving. These innovations are reshaping the way woodworkers approach design, precision, and scalability, while also sparking debates about the future of traditional techniques.
CNC (Computer Numerical Control) machines bring unparalleled accuracy to wood carving, enabling intricate patterns and repeatable designs that would be time-consuming or impossible by hand. From furniture detailing to architectural elements, CNC allows for mass production without sacrificing complexity. Meanwhile, 3D carving technology adds depth and dimension, creating lifelike sculptures and textured surfaces with digital precision.
Yet, these advancements raise questions about the role of human touch in woodworking. Traditional carvers argue that hand-carved pieces carry irreplaceable emotional value, with each chisel mark reflecting the artist’s skill and intent. Modern tools, however, empower smaller workshops to compete globally and reduce material waste through optimized cutting paths.
The most exciting development lies in the fusion of old and new—artisans using CNC for rough shaping before applying hand-finishing techniques, or designers combining 3D-carved bases with delicate manual detailing. This hybrid approach preserves heritage while embracing efficiency.
As the industry evolves, the key takeaway is balance: technology expands possibilities, but the soul of wood carving still thrives in the harmony between machine precision and human creativity.