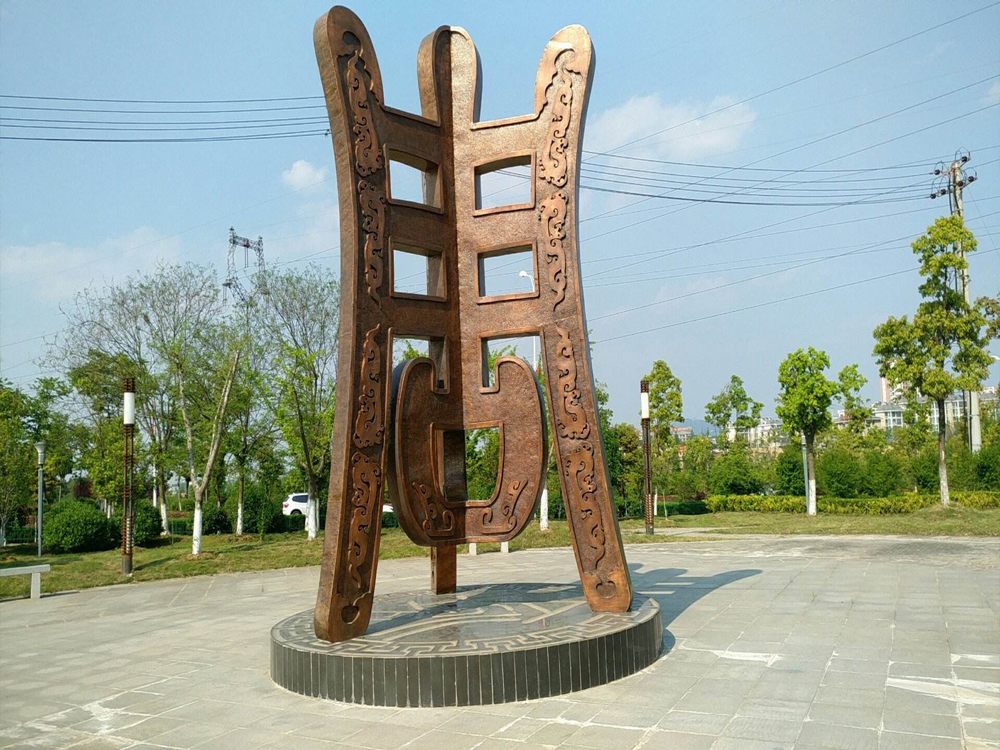
Wood carving requires precision and finesse, and the right abrasives and polishing techniques can make all the difference in achieving a smooth, professional finish. Here are the most common types of wood carving abrasives and polishing methods used by artisans:
1. Sandpaper Grits: Sandpaper is a staple in wood carving, available in various grits (from coarse to fine). Coarse grits (60-100) remove rough edges, while finer grits (220-400) refine the surface. Wet/dry sandpaper is ideal for wet sanding to minimize dust.
2. Steel Wool: Often used for delicate smoothing, steel wool comes in grades from #0000 (finest) to #3 (coarse). It’s excellent for curved or intricate designs where sandpaper might be cumbersome.
3. Buffing Compounds: Applied with a cloth or wheel, compounds like tripoli or white diamond polish the wood to a high shine. They work best after sanding to remove microscopic scratches.
4. Rotary Tools with Abrasive Attachments: Dremel tools with sanding drums, grinding stones, or polishing wheels allow detailed work on hard-to-reach areas.
5. Natural Abrasives: Pumice or rottenstone mixed with oil creates a traditional paste for hand polishing, yielding a deep, lustrous finish.
For best results, progress from coarse to fine abrasives and finish with a protective sealant. Mastering these techniques ensures your wood carvings stand out with a flawless, professional touch.